CONSTRUCTION
How Construction Estimators Contribute to Sustainable Building Practices
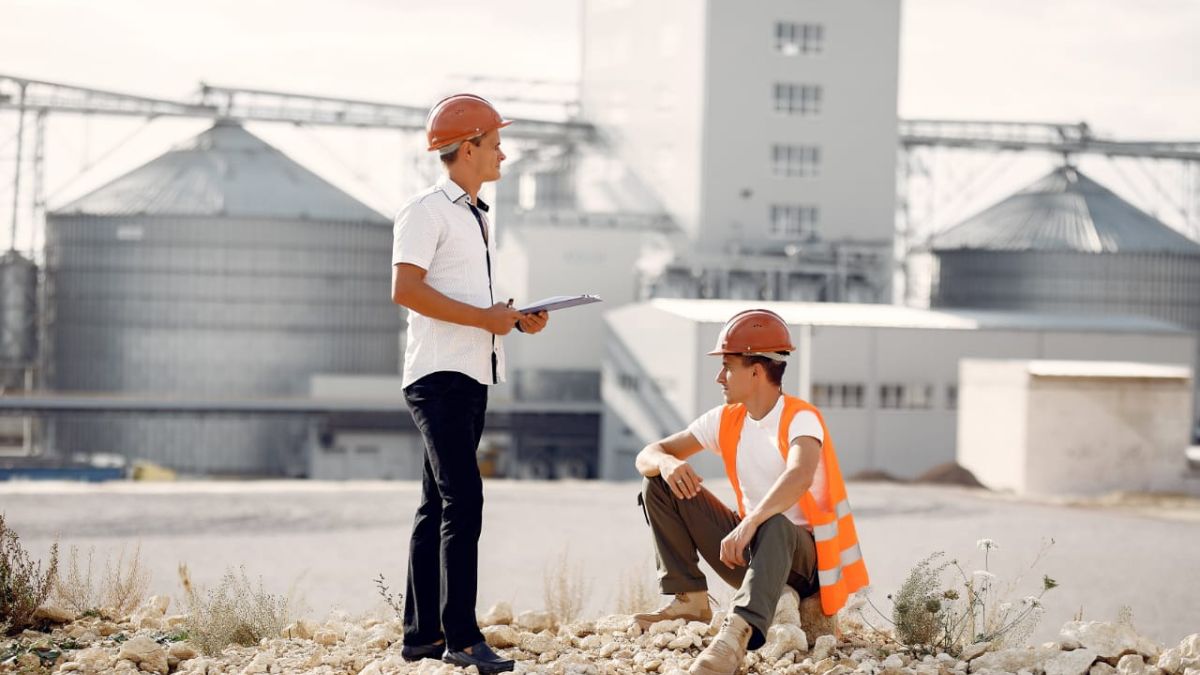
This paper focuses on the work of construction estimators within the construction industry and their contribution towards sustainable construction. Estimators are the specialists who bear the primary responsibility of predicting what costs and materials the construction project will need, which means they play a major role in determining the latter’s sustainability. Here are some of the key ways estimators contribute:
Material Selection
Drafting companies Estimators study and prepare to use recycled, and other sustainable materials that meet the project objectives and costs. In this way, they can provide a guarantee that only the appropriate sustainable materials were selected from different products available. Some of the recommendations that estimators may give are RCA, re-manufactured lumber, local material, and products with green labels. This diligence in the selection of building materials is very critical to the overall sustainability of the structures.
This paper aims to compare the capital cost between sustainable design features and conventional design features.
Some green design elements such as solar panels, efficient collection of stormwater, natural lighting, etc. need to be evaluated in detail on the financial impact. To ensure estimates are accurate, estimators will evaluate the ROI of systems and materials to be used and what is within the budget. Estimating is an important aspect of a project because it prevents early overspending on aspects that are not economically sustainable while at the same time, it can identify which systems are worthy investments. Facilitating these spending decisions and estimations helps more buildings to integrate sustainable features.
Waste Reduction Strategies
It is a depressing and shocking truth that construction waste contributes to over 35 % of the total landfill waste. As electrical estimating company estimators analyze the project plans and scope, they can develop helpful waste minimization strategies like:
- Executing reliable quantity surveys to order the right quantities of material to avoid excess purchases.
- Points that are associated with identifying opportunities where building materials can be reused instead of having to demolish buildings.
- Managing close coordination between only the just-in-time deliveries against the mass deliveries of perishable materials, for instance.
- Recycling waste material by having other uses for the waste material on other construction projects.
Evaluating Life Cycle Costs
Sustainable construction means considering total cost not only initial costs and not just the costs involved in the construction of the building. The estimators are responsible for estimating and comparing the cost over the life cycle of conventional and green materials and systems. Although such options have relatively higher initial costs, they prove to be worth the investment as they take years or even decades to pay themselves through the reduced cost of energy use and longer equipment life. Estimating teams engage in these projections to enlighten better long-term investment plans.
Constructability Recommendations
Many lumber takeoff services estimators do not merely look at figures in isolation, but they also consider the practicality of the construction work and the construction techniques. So that when they look at some of the plans they can identify areas that may be wasteful or inefficient in terms of sustainability. Estimators can then provide suggestions for using materials more efficiently, for sequencing operations in a way that reduces harm to the environment, or for altering designs to minimize the impact on the surroundings. Sustainability is also something that is frequently associated with value engineering.
Compliance Assistance
It is challenging to understand the distinctions in codes, standards, and certifications about green construction. Sustainability requirements can be met through help from estimators, who need to make sure their estimates include those requirements that apply to the project. This ensures project budgets and timelines factor in features such as LEED or Energy Star certification, Walgreens requirements, and other commissioning processes. Off-camera, the estimators continue to remind the team of possible compliance issues.
Smart Bid Analysis
Sustainability initiatives are highly dependent on contractors who either embrace the programs or show commitment and efficiency. The estimator teams must examine each contractor’s sustainability profile to understand how they can contribute to the project vision. Judging bid project experience, programs for waste management, green materials accessibility, and other issues reduces the risk of sustainability execution.
Ongoing Value Monitoring
Despite this, estimators, even if they have completed their estimates, still have a great deal of involvement in cost control and monitoring of performance on construction projects. They also play the role of checking on variance concerns on green features or guaranteeing that sustainability priorities are not overlooked amid construction. The fact that the estimator was overseeing these components ensured that the realized value was protected This feature ensured that the realized value was protected.
Partnering with Design Teams
Last but not least, estimators proactively consult and work hand in hand with architects, engineers, and designers from the conceptual stage of the project. Bringing the estimating lens early in the process means these teams can then test prices on various materials and systems which can be implemented before the design is complete. Estimators are delegated reliable members of the decision-making process on environmental and financial factors.
Conclusion
Estimating is not only about calculating the necessary financial amount that is needed for a project to go through. Estimators are poised to exert a great deal of influence over sustainability initiatives through their material selection knowledge, analysis of where green investments will provide the highest ROI, recommendations on reducing waste, experience in the use of life cycle costing, review of constructability issues, help with compliance, selection of contractors, monitoring of value delivery, and facilitation of collaboration between project teams. They help builders to achieve their visions and build sustainable architectures that are financially feasible.
Estimators need to apply the best practices in estimating purposefully toward the environment in a way that fosters cleaner, greener construction for the good of all. A focus on the building sector is seen to drive global sustainability forward at a good pace – and this has been aided significantly by the hardworking construction estimators working in the background.
CONSTRUCTION
Ways to pay for emergency home repairs
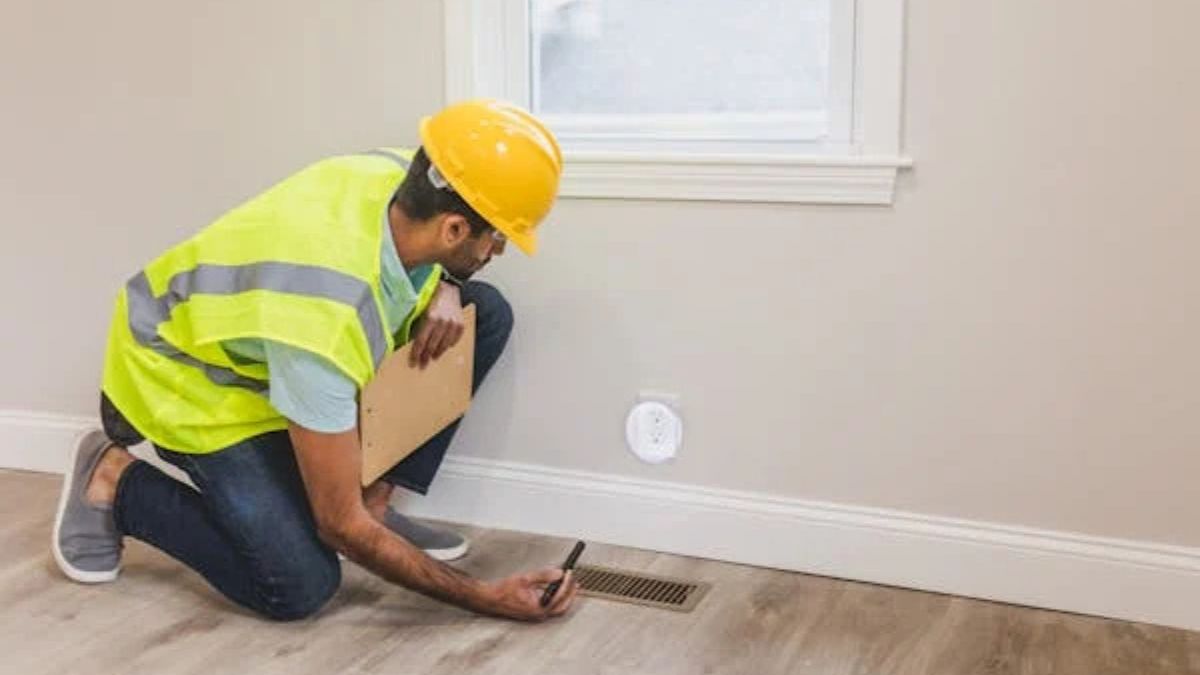
We’ve all been there – that unexpected moment when something in your home breaks down. One minute, everything is fine, and the next, you’re facing a major emergency repair. Whether it’s a busted furnace, a leaking roof, or a dead air conditioning unit in the middle of summer, these expenses can feel like financial punches that come out of nowhere. Water heater issues? Not too bad, right? A few hundred bucks, and you’re back to hot showers. But the larger expenses, like replacing a furnace or dealing with roofing issues, can throw a serious wrench in your budget. So, how do you cover those hefty costs? Here are several ways to finance emergency home repairs, and some of them might surprise you.
Look Into a Personal Loan
One of the most common ways to cover emergency home repairs is through a personal loan. If you have good credit, you might be able to borrow a lump sum of money from a bank or credit union. Personal loans are often unsecured, meaning you don’t have to put up your house or other assets as collateral, which makes them a safer option than some other loans. However, keep in mind that interest rates can vary depending on your credit score, so it’s important to shop around for the best rates.
Personal loans usually have a fixed repayment term, so you’ll know exactly how much you’ll owe each month. While this can help you budget and avoid surprise payments, it’s important to ensure you can afford the monthly payments before taking on this type of loan.
Home Equity Line of Credit (HELOC)
If you own your home and have built up some equity, a Home Equity Line of Credit (HELOC) might be an option for covering major repairs. This type of loan works similarly to a credit card: you’re given a credit limit, and you can borrow what you need, when you need it. The major difference is that a HELOC is secured by your home, so there is a risk if you fail to repay the loan.
While a HELOC can have lower interest rates than personal loans, it also requires you to use your home as collateral, which means you could risk losing your house if you can’t repay the loan. Make sure you can comfortably manage the payments before choosing this route.
Credit Cards: Not Always the Best, but an Option
Credit cards are often seen as a last resort for emergency expenses. That’s because interest rates on credit cards can be sky-high, especially if you carry a balance month-to-month. However, if you need to make a repair immediately and you have a credit card with a decent limit and a relatively low interest rate, it could be a quick fix.
Some credit cards also offer introductory 0% APR for a certain period, which can be a great option if you’re confident you can pay off the balance before the interest kicks in. However, if you can’t pay off the debt in time, the interest will hit hard, and you could end up paying far more than you initially borrowed.
Government Grants or Assistance Programs
For certain home repairs, especially those that affect your safety and health, there may be government assistance programs available. These programs are typically aimed at low-income homeowners or those who are elderly or disabled. For example, the U.S. Department of Housing and Urban Development (HUD) offers programs like the Section 504 Home Repair Program, which provides grants and loans to help homeowners make necessary repairs.
It’s worth doing some research to see if you qualify for any local, state, or federal programs. These grants and loans often don’t need to be repaid or come with very low-interest rates, making them a great option if you meet the eligibility requirements.
Home Repair Financing Through Contractors
Some contractors offer financing options for big repairs, like replacing your roof or furnace. These financing plans can be a good way to spread the cost of the repair over time, and some contractors offer interest-free financing for a set period. It’s a way to get the work done immediately without having to come up with all the money upfront.
However, it’s important to read the fine print carefully. If the financing offer seems too good to be true, it might come with hidden fees or extremely high-interest rates once the introductory period ends. Always do your homework and compare contractor financing with other available options to ensure it’s the best deal for your situation.
Homeowners Insurance
If the damage to your home is caused by a covered event (like a fire, storm, or vandalism), your homeowners insurance policy might cover some or all of the costs of repairs. Keep in mind that insurance will typically cover the repair or replacement of the damaged item (like a roof or furnace) after you meet your deductible.
For emergency repairs, homeowners insurance can be a life-saver, but it’s not always a guarantee that every issue will be covered. For example, if your furnace breaks down due to normal wear and tear, insurance is unlikely to cover the repair. It’s important to check your policy and contact your insurer to understand what’s covered in these situations.
DIY or Temporary Fixes
Sometimes, the best way to deal with an emergency home repair is to take a step back and assess the situation. Can you temporarily patch things up until you have enough funds to do a full repair? This is especially true for issues like plumbing leaks or roof damage. While it’s not a long-term solution, a temporary fix can buy you some time and allow you to save money for a permanent repair.
If you’re handy around the house, you might be able to tackle some minor repairs yourself. Fixing a leaky faucet or patching up a small hole in the roof could save you hundreds of dollars in labor costs. However, be careful about tackling larger, more complicated repairs unless you’re fully confident in your skills.
Final Thoughts
Emergency home repairs can be a real financial burden, but there are several ways to cover the costs without completely breaking the bank. Whether you’re considering a personal loan, using a credit card, tapping into your home equity, or applying for government grants, it’s important to weigh your options carefully and make sure you choose the one that best fits your financial situation.
Before making a decision, take a moment to assess your ability to repay the loan or credit, and explore any options that could help you minimize costs, such as government assistance or contractor financing. While home repairs are never welcome, with the right plan, you can get your home back in shape without causing financial strain.
CONSTRUCTION
Sustainable Roofing Solutions: Innovations and Practices in Commercial Roofing
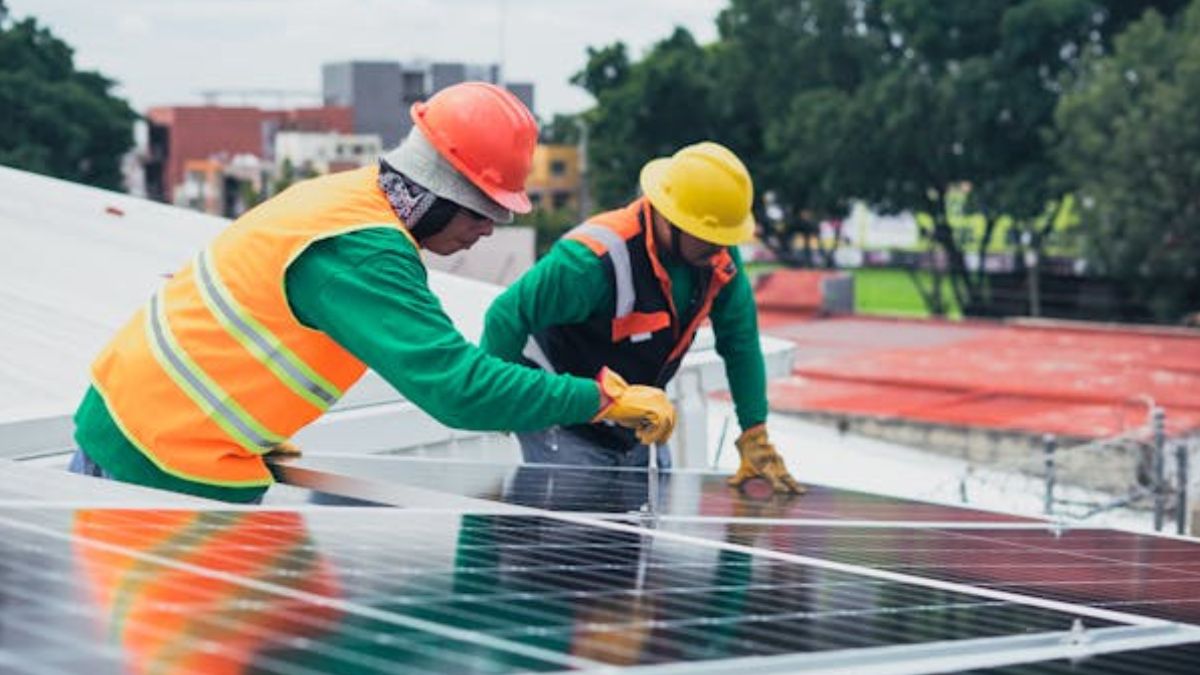
As the demand for environmentally friendly construction grows, the roofing sector is experiencing a considerable change. Nowadays, commercial roofing isn’t just about protection but innovation and sustainability. Modern roofing approaches focus on reducing energy consumption, enhancing building aesthetics, and improving the urban environment. From minimizing energy bills to lessening urban heat, sustainable roofing practices are shaping the future of our cities and businesses, making them more livable and efficient.
This guide delves into the various aspects of sustainable roofing solutions. Whether you are a business owner contemplating a roof replacement or an architect interested in the latest roofing trends, you’ll find valuable insights here. By exploring cutting-edge technologies, materials, and best practices that align with the growing environmental consciousness, it becomes clear how impactful these strategies can be. In an era where climate change is at the forefront of agendas, investing in sustainable roofing offered by a roofing company is not just an option; it’s an imperative.
Introduction to Sustainable Roofing
Sustainable roofing encompasses various materials and practices designed to minimize environmental impact. It includes using recycled materials, improving energy efficiency, and implementing innovative technologies. With buildings accounting for a significant amount of energy and resource use, the importance of sustainability cannot be overstated. These approaches help conservation efforts and lead to long-term savings and a healthier environment, contributing to a larger initiative in addressing climate change and resource depletion.
The Benefits of Green Roofs
Green roof roofs play a critical role in urban biodiversity, creating habitats for various species of birds, insects, and plants. They also enhance air quality by removing atmospheric pollutants and carbon dioxide. Moreover, green roofs reduce the urban heat island effect, making cities significantly warmer than surrounding rural areas. Green roofs can substantially curb temperature hikes in city centers, offering a cooler and more pleasant environment during scorching summers. This cooling effect makes urban living more comfortable and lowers the need for air conditioning, leading to energy savings.
Cool Roof Technologies
Cool roofs are made to reflect additional sunlight and take in less heat compared to a typical roof. It is achieved through reflective paint, cool roof tiles, or a reflective sheet covering. Cool roofs can decrease air conditioning needs by minimizing the heat taken in by the structure, particularly during peak summer months. The energy saved translates to reduced costs and diminishes the strain on power grids, which is critical for energy conservation efforts. Such technologies impact energy consumption, lowering utility bills and reducing greenhouse gas emissions. The benefits extend beyond individual buildings; the extensive implementation of cool roofs can aid in lower ambient temperatures in cities, mitigating the urban heat island effect.
Recyclable Roofing Materials
Investing in recyclable roofing materials is a smart, eco-friendly choice. Materials like metal, rubber, and certain polymers can be repurposed, decreasing the need for new raw materials. By choosing recyclable options, businesses contribute to what can be reused, reducing the demand for extra raw materials used more efficiently. Recyclable roofing options decrease landfill waste and can be a cost-effective choice as the initial installation costs are offset over time through their durability and minimal maintenance needs. Furthermore, these materials often boast superior longevity and lower environmental impact than conventional roofing materials, providing a win-win solution for sustainability.
Solar Roofing Integration
Solar panels integrated into roofing systems harness the sun’s energy to generate electricity. Solar roofs serve a dual purpose: providing shade and cooling to the building while generating clean energy. This integration enhances energy efficiency and embodies a commitment to renewable energy adoption. The result is reduced dependence on non-renewable resources and a significant cut in energy expenses. With advancements in photovoltaic technology, solar roofing has become more efficient and affordable for commercial applications. The enduring savings and ecological advantages make solar roofing a compelling and responsible option for contemporary companies.
Best Practices for Sustainable Roofing
Choosing the right sustainable roofing materials and contractors is crucial in ensuring effectiveness and durability. It starts with thorough research to ensure the materials used align with environmental standards and the local climate. Different regions may require specific roofing solutions to optimize performance and sustainability. Regular maintenance extends the roof’s lifespan and prevents costly repairs. It’s also beneficial to partner with experienced contractors specializing in sustainable practices, ensuring quality and efficiency. Engaging in continuous learning about emerging technologies and materials can empower businesses to make informed decisions that align with their sustainability goals.
Future Trends in Commercial Roofing
The commercial roofing industry is moving towards more interactive and intelligent systems. Smart roofing, incorporating sensors and automation for monitoring and maintenance, will likely become commonplace. These advanced systems enable proactive management of roofing health, identifying issues before they escalate and ensuring optimal performance. Additionally, as policies and regulations focus more on sustainability, innovation will continue to drive the development of new materials and techniques. Integrating AI and IoT in roofing solutions promises to revolutionize how commercial buildings manage energy and resources, enhancing sustainability and efficiency.
Conclusion
Sustainable roofing solutions offer myriad benefits, from cost savings to environmental preservation. Companies can establish a more sustainable future by adopting green practices and leveraging new technologies. The roofing evolution improves building efficiency while demonstrating a dedication to environmental responsibility. As awareness and technologies advance, the potential for positive impact through sustainable roofing becomes even more significant, paving the way for healthier communities and a resilient planet.
CONSTRUCTION
When is it time to renovate the electrical systems in your building?
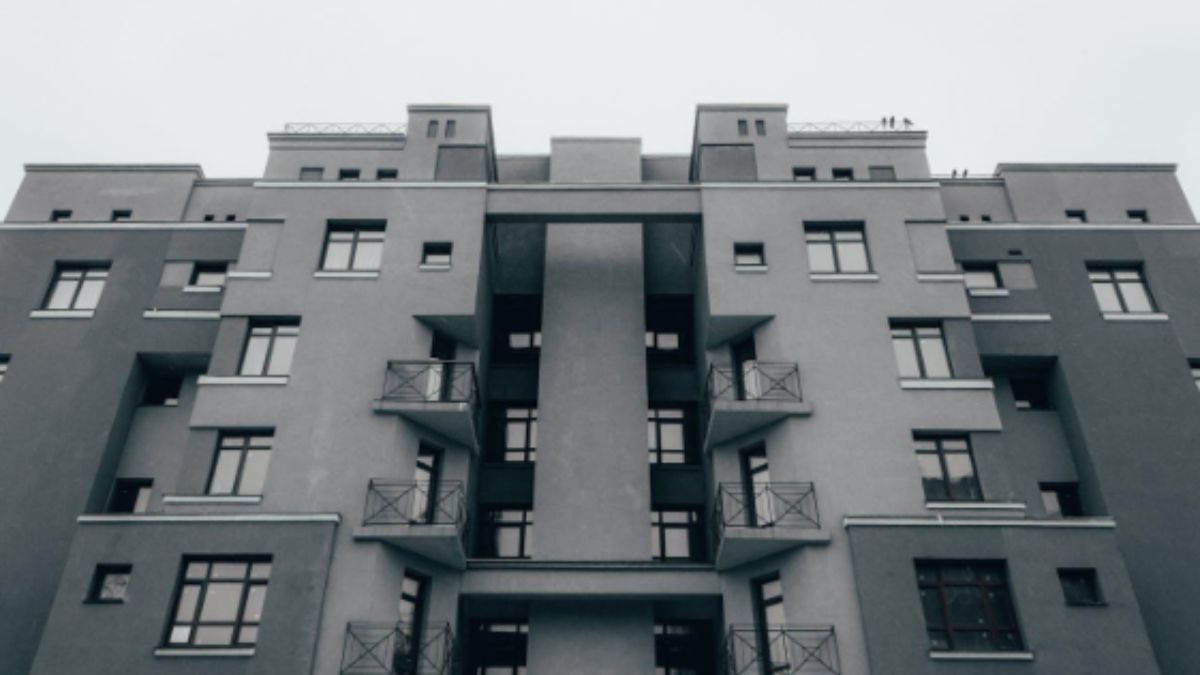
We often overlook the electrical systems in our buildings, focusing more on aesthetics or immediate repair needs. However, neglecting this crucial system can lead to significant issues, ranging from minor inconveniences to major safety hazards. Knowing when to renovate your electrical system is key to maintaining a safe and efficient property, ensuring that all components meet current demands and regulatory standards.
Choosing the right time for renovation
Timing your electrical renovation can be critical in minimizing disruption. Consider planning renovations during off-peak seasons or hours to reduce the impact on your tenants or business operations. Engaging experts from reputable property management companies in Montreal can help in smoothly navigating these renovations, ensuring that the process is efficient and the results are beneficial for all parties involved.
Recognizing the signs of an outdated electrical system
Electrical systems have a lifespan and exhibiting certain signs can indicate it’s time for a renovation. Flickering lights, frequent circuit breaker trips, and the use of multiple extension cords are clear signals. If your building is older and hasn’t had an electrical update in decades, it’s worthwhile to consult property management companies in Montreal who specialize in assessing such needs. These experts can provide a detailed evaluation and recommend whether a full or partial upgrade is necessary.
The role of technology upgrades
In today’s digital age, having an outdated electrical system can hinder the functionality of high-tech appliances and devices. If you find that your system struggles to keep up with the technological demands of tenants or business operations, it might be time to consider an upgrade. This not only improves efficiency but also attracts tech-savvy tenants or clients, enhancing your property’s appeal. Upgrading can also reduce energy consumption, contributing to a more sustainable operation.
Safety concerns that demand immediate action
Safety should always be the top priority. Signs of electrical problems such as burning smells, visible burns on outlets, or shocks from electrical devices are urgent cues that your building’s electrical system needs attention. Such issues are not only hazardous but could potentially lead to severe accidents or fires if not addressed promptly. Immediate renovations can restore safety and give peace of mind to all building occupants.
Evaluating the impact of regulatory compliance
Regulations regarding building safety and electrical standards often change. Staying compliant is crucial not only for safety but also to avoid legal penalties. Renovating your electrical system to meet current codes and standards can save you from future troubles and significant financial liabilities. Compliance ensures that your property adheres to the latest safety norms, which is essential for insurance and real estate value.
Planning for the future: scalability and flexibility
As your building ages, its needs will evolve. Planning a renovation with scalability in mind ensures that the electrical system can handle future upgrades and changes. This foresight can be especially beneficial in rapidly developing areas, or in buildings expected to experience growth in tenant capacity or technological use. Designing a flexible system allows for easy updates, which can be crucial for adapting to technological advancements and increasing demand.
Renovating your building’s electrical system is a major undertaking, but it’s an essential one for the safety, efficiency, and longevity of your property. With the right planning and expert advice, you can ensure that your property remains up to date and compliant with all safety regulations. Act now to secure your investment and safeguard your occupants.
-
HEALTH1 year ago
Integrating Semaglutide into Your Weight Loss Plan: A Practical Guide
-
HOME IMPROVEMENT1 year ago
How to Choose the Perfect Neutral Area Rug for Every Room
-
LAW1 year ago
Teenage Drivers and Car Accidents in California: Risks and Parental Liability
-
LAW1 year ago
Post-Divorce Considerations in California: Modifications and Long-Term Planning
-
CONSTRUCTION1 year ago
Construction Site Safety Regulations in New York and Your Rights as a Worker
-
HOME1 year ago
Sandra Orlow: The Teen Model Who Captivated the Internet
-
FINANCE1 year ago
Digital Asset Management in Florida Estate Planning
-
LAW1 year ago
Kentucky’s School Football: Concussions, Injuries, and Legal Options