CONSTRUCTION
Construction Site Safety Regulations in New York and Your Rights as a Worker
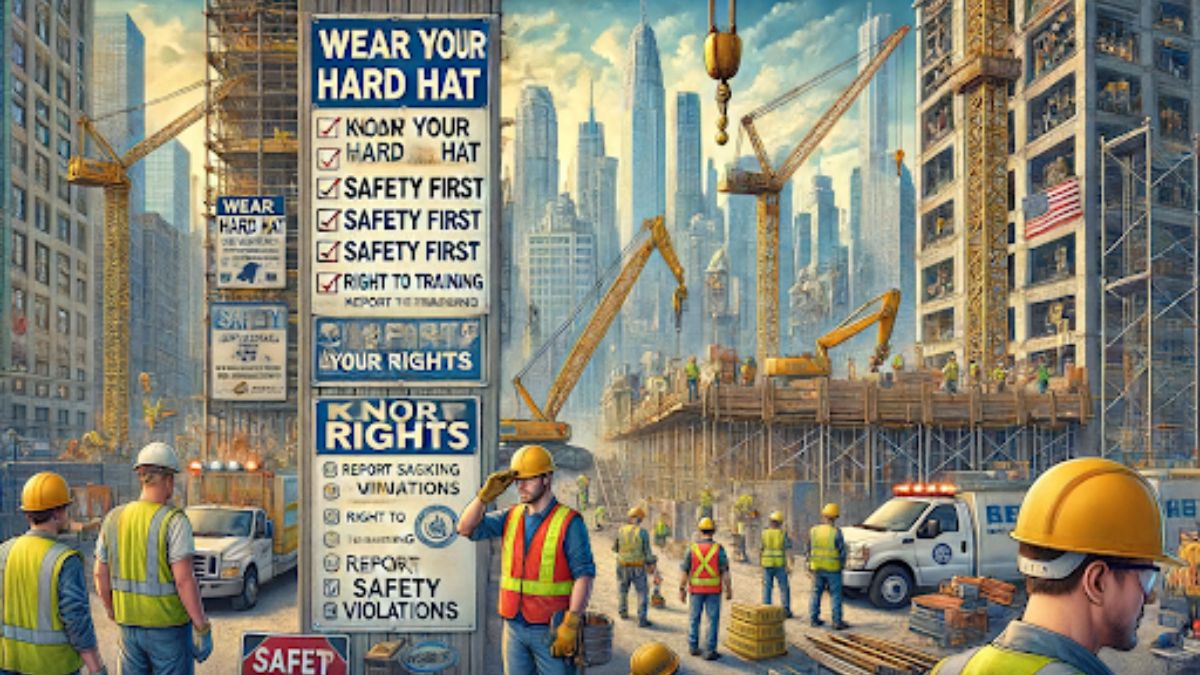
Construction site safety regulations in New York are stringent and essential for the well-being of workers and the public. The New York City Department of Buildings implements Chapter 33 of the NYC Construction Codes, which outlines safety requirements, including bans on smoking at construction sites and other crucial regulations. Workers have the right to a safe workplace, free from known dangers, under the Occupational Safety and Health Act of 1970.
In New York City, safety is taken seriously, and injured workers have legal support available from New York construction accident lawyers. The New York Labor Code also offers specific protections, such as safeguards against various hazards, including slip, trip, and fall incidents. These regulations ensure that employers are held accountable for maintaining a safe working environment.
Understanding your rights as a worker can prevent severe injuries and save lives. Employers are required to follow these safety rules, and workers should be aware of the protections afforded to them. By adhering to OSHA requirements, such as providing safe working conditions, employers can significantly reduce the risk of accidents on construction sites.
Understanding New York Construction Site Regulations
New York imposes stringent safety regulations to ensure the well-being of construction workers and the public. The framework includes detailed construction codes, safety training requirements, and defined roles for all parties involved in a construction project.
Overview of Chapter 33 and NYC Construction Codes
Chapter 33 of the NYC Construction Codes mandates comprehensive safety measures. These include regulations on structural stability, fall protection, and hazardous materials handling. Smoking is banned on construction sites to reduce fire hazards.
The 2014 NYC Construction Codes specifically address safeguards like safety railings, netting, and controlled access zones. Regular inspections are conducted to ensure compliance, and violations can result in severe penalties for contractors and employers.
Safety Training Requirements and Compliance
Site Safety Training (SST) is compulsory for construction workers in New York. To obtain an NYC SST Card, workers must complete approved courses, including OSHA 10 or 30, fall protection, scaffolding, and electrical safety.
Under Local Law 196, all workers must have at least 40 hours of training, while supervisors require 62 hours. Compliance is verified by the NYC Department of Buildings, and failure to meet training requirements can lead to significant fines and work stoppages.
Roles and Responsibilities on the Job Site
Several key roles ensure safety on construction sites. Construction superintendents oversee the entire project, while site safety coordinators and managers specifically focus on compliance with safety regulations.
Employers and contractors must provide the necessary equipment and training. They are also responsible for maintaining a safe working environment. Workers must adhere to all safety rules and wear the required protective gear.
Personal Protective Equipment and Safeguards
Personal Protective Equipment (PPE) is essential for minimizing risks. Standard PPE includes helmets, gloves, safety goggles, and high-visibility clothing. Fall protection gear like harnesses and safety nets are also mandatory.
Safeguards like barricades and warning signs help prevent unauthorized access to hazardous areas. Employers must ensure that all protective gear and safety systems are regularly inspected and maintained.
Regular safety drills and emergency response plans are also crucial in preparing for unforeseen incidents.
Your Rights and Resources as a Construction Worker
Construction workers in New York have specific rights to ensure their safety and well-being on the job. Understanding these rights and knowing how to take action when violations occur are critical components for every worker. Access to legal resources and pathways to compensation are also crucial.
Understanding Worker Rights and OSHA Standards
Construction workers in New York are protected under OSHA standards. These standards, enforced by the Occupational Safety and Health Administration, set strict guidelines to ensure safety at job sites. Workers have the right to a safe workplace and can report unsafe conditions without fear of retaliation. Key rights include the following:
- The right to receive training in a language and vocabulary they understand.
- The right to review records of work-related injuries.
- The right to request an OSHA inspection if they believe their workplace is unsafe.
What To Do in Case of Safety Violations or Accidents
If a worker identifies a safety violation or is involved in an accident, several steps must be followed. Immediate reporting to a supervisor is essential, followed by documenting the conditions that led to the violation or accident. Filing a complaint with OSHA can trigger an investigation. Construction workers should keep the following in mind:
- Promptly notify a supervisor about the issue.
- Document everything, including taking photos and gathering witness statements.
- File a formal complaint with OSHA, which protects against employer retaliation.
Accessing Legal Assistance and Compensation
Construction workers have numerous legal resources available if they are injured or if their safety rights are violated. Organizations and other NYC construction accident lawyers specialize in these cases, providing guidance and representation. Compensation claims can cover medical bills, lost wages, and pain and suffering:
- Contact a specialized construction accident lawyer.
- Gather all documentation related to the injury, including medical records and accident reports.
- Know your rights under New York’s labor laws to secure appropriate compensation.
In Conclusion
Adhering to construction site safety regulations is vital for ensuring the well-being of workers in New York. The New York Public Employee Safety and Health (PESH) Bureau, along with OSHA, plays a significant role in overseeing safety compliance.
Workers have protection under laws such as NY Labor Law 241, which includes Section 23. This section specifically covers safety standards for construction, demolition, and excavation activities.
Property owners, contractors, and site managers are mandated to maintain safe work environments. Regulations such as the NYC Building Code 3303.7.3 prohibit activities like smoking on construction sites to minimize risks.
Key Points:
- Regulations: Governed by PESH and OSHA
- Worker Protections: NY Labor Law 241, Section 23
- Safety Standards: NYC Building Code 3303.7.3, among others
By understanding these regulations and protections, workers and employers can contribute to a safer construction industry in New York City.
CONSTRUCTION
Selecting the Perfect Flooring for Your House; Helpful Suggestions
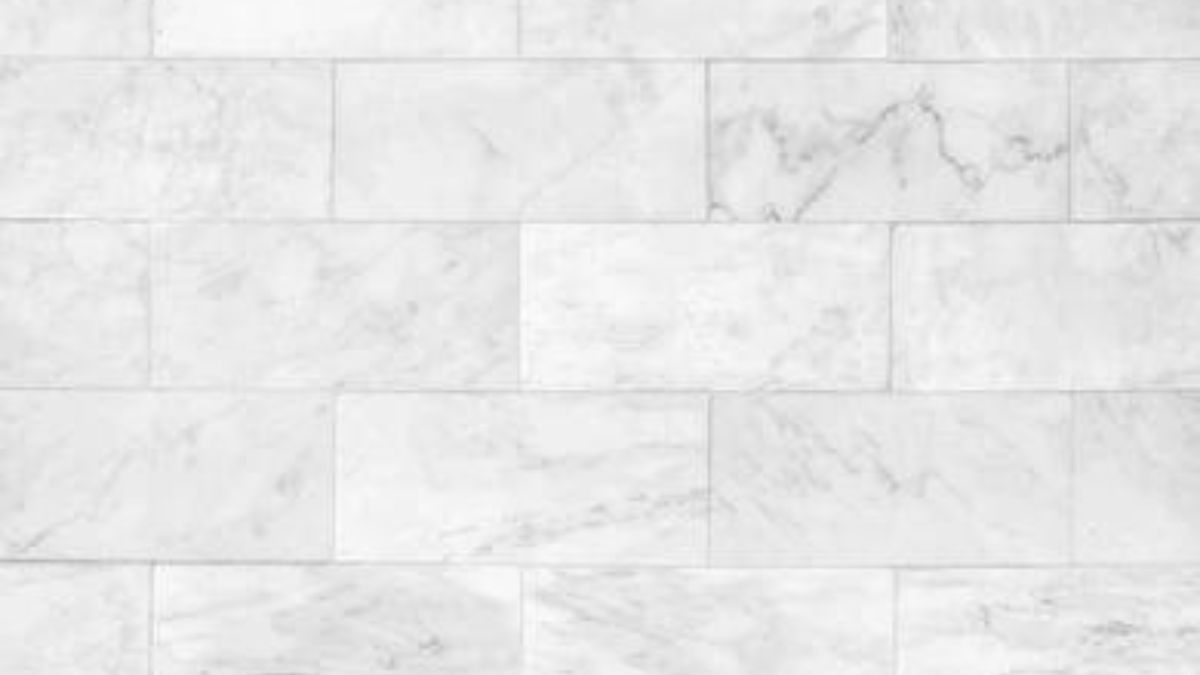
When deciding on the flooring for your rooms or areas within your home or office space to consider, think about how durable and practical it is for your needs and personal taste preferences as well as how easy it is to keep clean and maintain its appearance over time. Take into account factors like how foot traffic the area receives regularly and whether the flooring material is resistant to moisture damage so that you can enjoy a lasting investment in your space that meets both your practical requirements and aesthetic desires. Whether you opt for hardwood floors to add warmth and character to a room or choose vinyl for its low maintenance qualities or even go with tile for a chic finish. It’s important to strike a balance, between functionality and style that complements your unique needs perfectly.
Choosing the type of flooring is crucial for any space
Installing flooring in your home can make an improvement, in both its look and functionality – not enhancing the overall ambiance but also positively influencing the long term value of your property as well! Research from HGTV indicates that certain flooring types can significantly boost a homes resale value, for homeowners seeking tile installation near me could be a crucial choice that ensures their investment is worthwhile.
Choosing thoughtfully is key, for long term satisfaction. Maximizing the value of your investment in the run. Select the type of flooring you want carefully as it can affect factors such, as comfort and maintenance costs over time. Therefore it’s crucial to evaluate all factors before deciding on a material or style. Neglect of this decisions significance could lead to discontent in the increased maintenance needs that may raise your costs and efforts down the line.
Different Types of Flooring Materials
When deciding on the flooring for your space, you’ll come across options each with its own advantages and disadvantages to weigh in consideration. Hardwood floors are well liked for their durability and aesthetics. Require care to avoid scratches and wear. Laminate flooring offers a look at a price point and is known for being easy to install and upkeep. Tile is an option ideal for areas with heavy foot traffic or moisture concerns such, as bathrooms and kitchens. Vinyl flooring is recognized for its ability to resist water and its low maintenance needs but keep in mind that priced options may not have a lifespan. Carpet provides a feeling underfoot. Is great, for bedrooms and living areas to enhance the atmosphere while also offering insulation from chilly weather outside.
Aspects to Take into Account
When you’re choosing flooring options to enhance your living space or renovate your homes, look and feel in mind several aspects play a role in making the decision. To start with setting a budget is crucial to stay on track and make spending choices that fit within your means while still achieving the desired quality standards for your floors. Considering the level of foot traffic areas of your living space endure is important as it determines the durability requirements for flooring materials such as hardwood or tile which are better suited for trafficked zones whereas carpet might be more suitable for bedrooms or areas with less frequent use. Factor in the time and effort needed for cleaning and maintenance as flooring materials come with varying upkeep needs which can impact your routine and lifestyle. Moreover, take into account your homes climate conditions and humidity levels when selecting flooring types as some wood varieties may be prone to warping in environments ultimately affecting their longevity in settings. On the other hand, pricier materials such as tile or laminate may fare better in regions. By taking these factors into account, you can be confident that your flooring will maintain its appearance and durability despite the conditions and obstacles in your home environment.
Living House Flooring
When selecting your flooring type consider how it matches your life— its ability to last long and feel right and the effort it needs for strife. For owners seeking the best go for materials to clean and scratch proof like tile or vinyl without any jest to handle your furry friends on the roof. Families with kids at play should opt for carpets soft creating a cozy spot where laughter may sway without worries of damage aloft. For those who love to host and entertain, choose from luxurious tiles that are grand, and resilient to spills and wear with no strain while keeping elegance at hand. Choosing the flooring that fits your lifestyle is essential to make sure it can withstand your routines and stay in good shape as time goes by.
Tips for Keeping Things in Good Working Order
Taking care of your flooring is important to keep it looking great and lasting term. To maintain hardwood floors’ beauty and durability, regular maintenance is essential. To care for them properly, remember to sweep and use a combination of a mop and wood cleaner to preserve the finish without risking any damage from excess water or harsh furniture pads. For keeping your floors clean, use a brush or broom for sweeping and a slightly damp mop for tackling tougher stains without causing harm or encouraging mold growth in the grout lines. Don’t forget to vacuum to get rid of any dirt or dust buildup on your floors and carpets! Make sure you follow the manufacturers recommendations for taking care of your carpet ! It’s really important to vacuum and clean your carpets on a basis – consider using a carpet cleaner every six months to a year. Be sure to deal with spills promptly to prevent stains from becoming permanent! Don’t overlook rotating your rugs for even wear distribution! By keeping up with maintenance tasks, like these you not enhance the appearance and comfort of your home but also extend the life of your flooring materials.
Recent Advances and State of the Art Progressions
The world of flooring is evolving with eco options, like bamboo and cork, gaining popularity alongside recycled hardwood due to the industrys increasing focus sustainability concerns are driving this trend forward. Additionally, tiles and moisture detecting sensors are becoming popular for their comfort and early warning of water damage issues making them attractive to consumers. Patterns and vibrant color choices are also making a comeback in home decor to reflect design trends. Websites, like Houzz, provide information on flooring trends to help homeowners choose options that match their style preferences and technological needs effectively. Keeping up, to date with these trends can empower homeowners to make well informed choices regarding their flooring selections.
CONSTRUCTION
How to Ensure Quality Craftsmanship from Remodeling Contractors
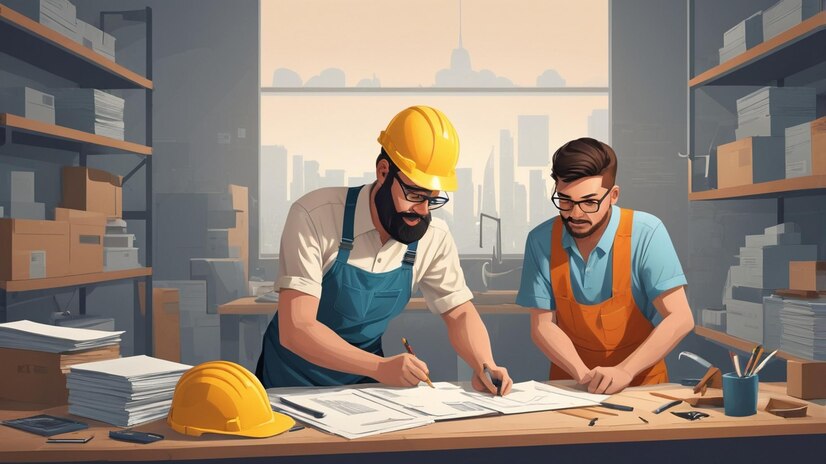
Ensuring quality craftsmanship from remodeling contractors is key to a successful home upgrade. You want your remodel to not only look great but also stand the test of time. Finding the right contractor can be a game-changer, transforming your vision into reality with skill and precision.
In this guide, we’ll walk you through easy steps to help you select the best contractor and make sure your project turns out just the way you imagined. From research tips to final inspections, we’ve got you covered so you can enjoy a beautiful and lasting remodel.
Research and Vetting Process
Finding quality craftsmanship starts with a solid research and vetting process. This step is crucial because it helps you identify reliable remodeling contractors who can turn your vision into reality. Here’s how you can make sure you’re choosing the right professionals for the job.
Researching Contractors
Begin by looking up contractors online. Sites like Google, Yelp, and Houzz are great for checking out reviews and ratings. Pay attention to what past customers say about their experiences. Also, ask friends, family, and neighbors if they have any recommendations. Personal referrals can be very trustworthy.
Checking Credentials
Next, make sure your potential contractors are licensed and insured. This means they have the proper qualifications and protection for their work. You should also look for any industry certifications or memberships, which can show a commitment to their craft.
Reviewing Past Work
Take a close look at the contractor’s portfolio. This will give you an idea of their style and quality. Don’t hesitate to ask for references from previous clients. Contact them to find out if they were happy with the work and if the contractor met their expectations.
Detailed Project Planning
Detailed project planning is crucial for ensuring quality craftsmanship forms contractors for home remodeling. It lays the groundwork for a smooth and successful renovation by clearly defining your goals and expectations. Here’s how to set everything up for a fantastic outcome.
Clear Communication
Start by communicating your project goals clearly. Make sure you and your contractor understand each other’s expectations. Discuss every detail of the remodel, including design choices, materials, and any special features you want. This helps prevent misunderstandings and ensures that the finished work matches your vision.
Creating a Timeline
A well-defined timeline is crucial for keeping your project on track. Work with your contractor to establish realistic deadlines for each phase of the remodel. This includes start and finish dates, as well as key milestones along the way. Having a clear schedule helps avoid delays and keeps the project moving smoothly.
Budget and Cost Estimates
Discuss the budget openly with your contractor. Ask for a detailed cost estimate that breaks down all expenses, including materials and labor. Understand what’s included in the quote and be prepared for any potential changes. Clear budgeting helps prevent unexpected costs and keeps the project within your financial limits.
With detailed project planning, you’ll set up a solid foundation for your remodel. It helps ensure that everything goes as planned and that you’re happy with the final results.
Selecting the Right Materials
Selecting the right materials is key to ensuring quality craftsmanship from remodeling contractors. The materials you choose can make a huge difference in both the look and durability of your remodel. Here’s how to make smart choices for your project.
Quality vs. Cost
First, think about balancing quality and cost. While it might be tempting to go for cheaper options, investing in high-quality materials often pays off in the long run. They tend to last longer and look better, which can save you money on repairs and replacements down the road. Look for materials that offer good durability and fit within your budget.
Contractor’s Material Choices
Your contractor will likely suggest materials based on their experience. Listen to their recommendations, but also do your own research. Ask why they prefer certain materials and if there are any alternatives that might be better for your needs. It’s important that you understand the benefits and drawbacks of each option before making a decision.
Alternative Options
If you’re considering alternative materials, discuss them with your contractor. For example, if you prefer a specific type of flooring or countertop, check if it fits your remodel’s design and functionality. Sometimes, a slightly higher cost for a better option can lead to a more satisfying result.
Choosing the right materials ensures your remodel not only looks great but stands the test of time. Making informed decisions will help you achieve a beautiful and lasting outcome.
Contract and Legal Aspects
Understanding the contract and legal aspects is crucial for ensuring quality craftsmanship from remodeling contractors. A well-drafted contract protects both you and the contractor, making sure everyone is on the same page. Here’s what you need to know to keep your project smooth and secure.
Written Agreements
First, always get a written contract. This document should clearly outline the scope of work, including detailed descriptions of the project, materials, and costs. Make sure it also includes a timeline with start and finish dates. A detailed contract helps avoid misunderstandings and ensures that both parties know what to expect.
Change Orders
During the remodeling process, changes might come up. Any changes to the original plan should be documented through change orders. This means that if you decide to add or remove something, it’s formally agreed upon and reflected in the updated cost and schedule. This keeps the project organized and prevents surprise expenses.
Warranties and Guarantees
Lastly, check the warranties and guarantees offered by your contractor. A good warranty covers workmanship and materials for a specific period. Make sure you understand what is covered and for how long. A strong guarantee shows that the contractor stands by their work and is committed to quality.
By focusing on these contract and legal aspects, you’ll protect yourself and ensure that your remodeling project goes off without a hitch. It’s a key step in achieving quality results and a successful remodel.
Monitoring the Remodeling Process
Monitoring the remodeling process is essential for ensuring quality craftsmanship from your contractors. Keeping a close eye on the project helps you catch any issues early and keeps everything on track. Here’s how to stay involved and ensure your remodel turns out just as you envisioned.
Regular Check-ins
Start by scheduling regular check-ins with your contractor. Visit the site frequently to see the progress and make sure the work aligns with your plans. During these visits, pay attention to the details and ask questions if anything seems unclear. Consistent monitoring helps ensure that any problems are addressed quickly.
Communication with the Contractor
Good communication is key to a smooth remodeling process. Maintain an open line with your contractor, and make sure you both are on the same page about the project’s progress. Share your feedback and address any concerns as they arise. Clear communication helps prevent misunderstandings and keeps the project moving smoothly.
Addressing Issues Promptly
If you notice any issues or deviations from the plan, address them as soon as possible. Whether it’s a minor detail or a major concern, bringing it up early allows your contractor to fix it before it becomes a bigger problem.
Prompt action helps ensure the final result meets your expectations.
By monitoring the remodeling process closely, you’ll help ensure that your project stays on track and meets your quality standards. Active involvement and clear communication are key to achieving the best results.
Final Inspection and Approval
Final inspection and approval are crucial steps in ensuring quality craftsmanship from your remodeling contractors. This is the moment when you review the completed work to make sure everything meets your expectations and matches what was agreed upon. Here’s how to make sure the final result is just right.
Quality Checks
Begin by thoroughly inspecting the finished work. Look at every detail, from the overall appearance to the finer touches. Check that all the materials and finishes are as specified in your contract. It’s helpful to use a checklist of the agreed-upon features to make sure nothing is overlooked.
Professional Inspections
In some cases, it’s worth hiring a third-party inspector to review the work. This can be especially useful for complex projects. A professional can spot any issues that might not be immediately obvious and provide an objective assessment of the quality. This step ensures that everything is up to code and functioning properly.
Final Payment and Closure
Once you’re satisfied with the work, it’s time to handle the final payment. Make sure all the terms of the contract have been fulfilled before making this last payment. Confirm that any final paperwork is completed and that you have all necessary documentation, like warranties and guarantees.
By carefully managing the final inspection and approval process, you ensure that your remodeling project ends on a high note. This careful review guarantees that you get the quality craftsmanship you’ve been promised.
Post-Project Care and Maintenance
Post-project care and maintenance are essential for ensuring quality craftsmanship from your remodeling contractors lasts for years to come. Once your remodel is complete, taking care of your new space helps keep it looking and functioning like new. Here’s how to keep your remodel in top shape.
Maintaining Quality
Start by following any care instructions provided by your contractor or the manufacturers of the materials used. Regular cleaning and proper maintenance can prevent wear and tear and keep your remodel looking fresh. For instance, clean surfaces with recommended products and avoid any harsh chemicals that could damage finishes.
Contractor Follow-Up
Even after the project is finished, stay in touch with your contractor. Many contractors offer a warranty period during which they can fix any issues that arise. If you notice any problems or have questions, reach out to them. It’s a good idea to keep a record of any maintenance or repairs needed for future reference.
Future Projects
Maintaining a good relationship with your contractor can be beneficial for any future projects. If you’re happy with their work, they could be your go-to professional for upcoming renovations. Plus, they’ll already be familiar with your home and preferences, making future projects smoother.
By focusing on post-project care and maintenance, you’ll extend the life and beauty of your remodel. Proper upkeep ensures you get the most out of your investment and enjoy your
Conclusion
In conclusion, ensuring quality craftsmanship from remodeling contractors is all about careful planning and clear communication. By following these steps, you’ll be well on your way to achieving a stunning remodel that meets your expectations. Take charge of your project, and watch your dream space come to life!
CONSTRUCTION
DIY vs. a roofing contractor: Which is the right choice?
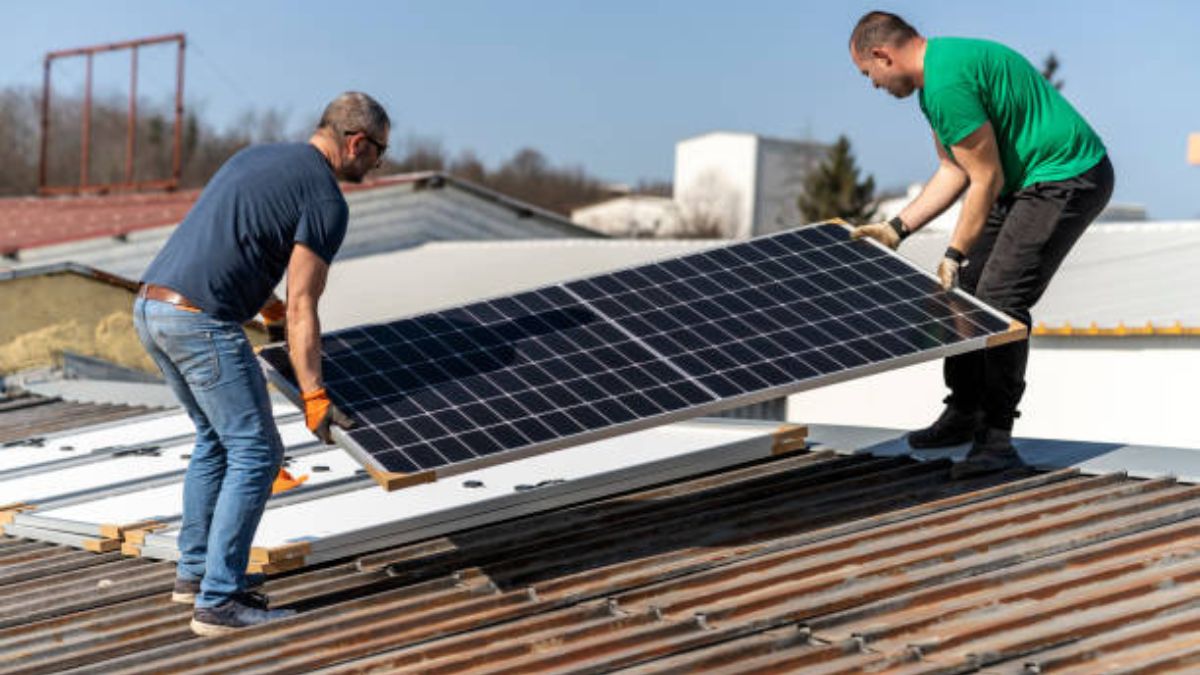
With so many reference materials on DIY roofing hacks, you might feel confident enough in those tutorials that calling a professional remains a mere second option.
But regardless of anything, you cannot overlook the experience and expertise a roofing contractor, like Tadlock Roofing, will bring to you. These professionals have hands-on experience dealing with different types of roof structures and possess the skills and equipment required for any work on your roof.
So, before you jump straight into choosing your option, knowing the differences between DIY roofing and hiring a professional contractor is important.
Benefits of DIY roofing projects
- You will be your own master. You have the freedom to choose the roofing materials or decide the course of action to be taken in a DIY project.
- Supervision will be at your discretion, meaning that you will be the sole person who will monitor the entire project without the involvement of any third party.
Benefits of hiring a professional roofing contractor
With a professional roofing contractor, you won’t have to worry about the quality of the roofing materials or the overall repair and replacement tasks. They will leverage their experience and expertise to complete the project and cater to your specific requirements.
Furthermore, these professionals are licensed and certified, meaning they have the necessary skills and knowledge to work with different tools and roofing materials prevalent in the market.
Although the upfront investment may be a bit high, it will be worth it since you won’t have to spend any more money on the roof structure in the coming years.
Analyzing DIY vs. roofing contractors: factors to consider
To understand the differences between a DIY roofing project and hiring a professional contractor, we have prepared a comparison study below.
Cost factor
- DIY roofing project: Upfront investment will be less, and you can manage the flow of funds by choosing cheaper or more cost-effective materials. Besides, you won’t have to pay any fees to a third party.
- Professional roofing contractor: The cost may be comparatively higher, but it will be worth the investment in the long run.
Time considerations
- DIY roofing project: Since you will be responsible for all the tasks, from material procurement to quality assessment, DIY projects will take a while to complete.
- Professional roofing contractor: On the contrary, a professional roofing contractor can leverage their knowledge and expertise to bridge the time requirement while ensuring uncompromised quality.
Safety protocols
- DIY roofing project: You won’t know about the safety requirements to be met while working on the roofing structure. Besides, you might not even have the necessary safety and security equipment.
- Professional roofing contractor: A professional contractor will be aware of all the safety standards to be met, and they will use the required tools and equipment to reduce workplace injuries and accidents.
Impact on property valuation
- DIY roofing project: Poor execution of the DIY project will severely impact the property value and spoil the overall aesthetics.
- Professional roofing contractors: These experts will ensure the property value is enhanced through proper planning and execution and optimal quality assurance.
Conclusion
Deciding between hiring a professional roofing contractor or undertaking a DIY roofing project is not easy. But with the guidance above, you will have clarity about the pros and cons of both of these decisions. So, make your choice accordingly while keeping the long-term benefits in mind.
-
HEALTH5 months ago
Integrating Semaglutide into Your Weight Loss Plan: A Practical Guide
-
HOME IMPROVEMENT5 months ago
How to Choose the Perfect Neutral Area Rug for Every Room
-
ENTERTAINMENT1 month ago
Inside a Coomer Party: A Closer Look at this Growing Trend
-
LAW4 months ago
Teenage Drivers and Car Accidents in California: Risks and Parental Liability
-
FASHION5 months ago
7 Celebrity-Inspired Elegant Summer Dresses For 2024
-
LAW4 months ago
Gang Activity and Criminal Charges in CA: Protecting Your Rights
-
LAW4 months ago
Kentucky’s School Football: Concussions, Injuries, and Legal Options
-
LAW4 months ago
Post-Divorce Considerations in California: Modifications and Long-Term Planning