INDUSTRY
Revolutionizing Industries: The Power of Industrial Casters
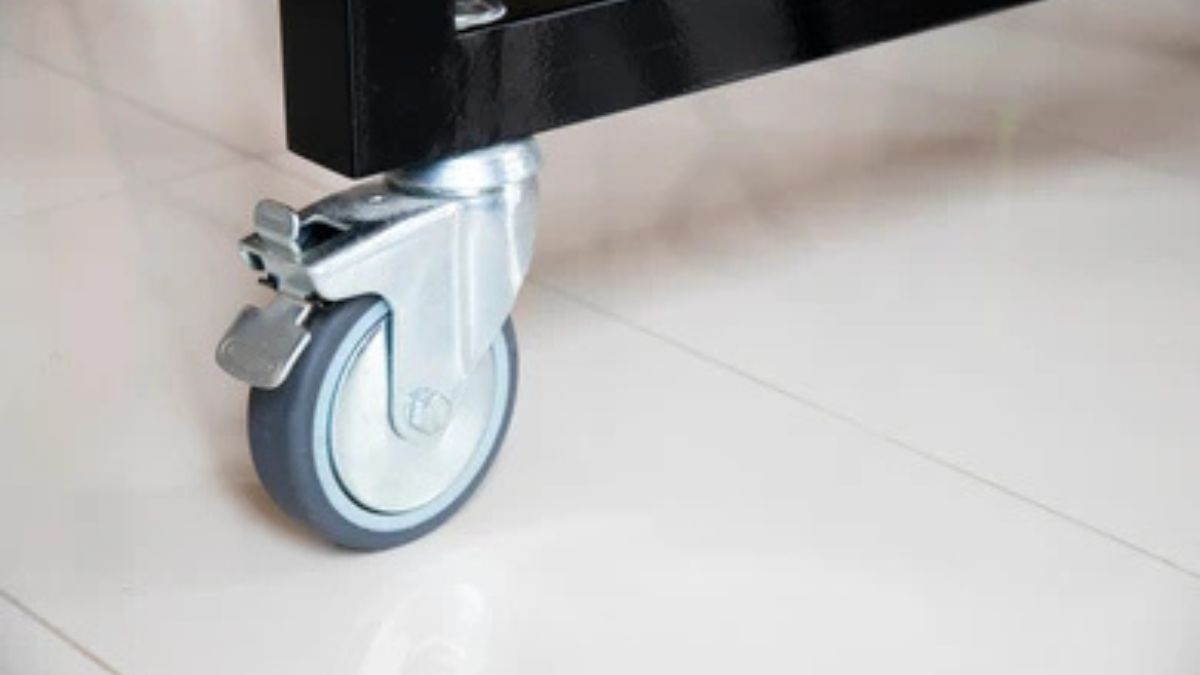
In today’s fast-paced industrial landscape, efficiency and mobility are paramount to success. The humble caster is one often overlooked yet essential component that enhances operational productivity. These small wheels are not just functional accessories; they are transformative tools that facilitate the movement of heavy equipment, machinery, and furniture in various settings. Suitable casters can significantly streamline workflows, reduce workplace injuries, and improve overall efficiency from manufacturing plants to warehouses. As industries evolve and adapt to new challenges, understanding the capabilities and innovations in caster technology can lead to more innovative solutions and enhanced operational performance.
Casters and Their Importance
Industrial casters have long been an unsung hero in the background of countless industries. These humble wheels often go unnoticed and play a critical role in enhancing the mobility and functionality of various systems and facilities. From the early 20th century, casters have evolved significantly from simple fixed wheels to sophisticated, high-tech components. Today, they are indispensable in numerous settings, providing solutions that improve mobility and enhance safety and productivity.
A particular standout is the application of small shock absorbing casters, which absorb vibrations and reduce impact, thereby extending the lifespan of floors and equipment. This innovation is especially noteworthy in sectors where precision and equipment maintenance are critical, offering operational efficiency and cost savings by minimizing damage.
Common Applications in Various Industries
The versatility of casters is evident in their widespread application across various industries. For instance, in the healthcare sector, medical carts and equipment are fitted with casters to facilitate the swift movement of essential supplies and devices around hospital wards. This ensures that patient care is delivered without delay and reduces physical strain on healthcare workers, enhancing their efficiency and reducing workplace injuries.
In retail environments, casters are integral to the flexibility of store layouts. Shelves and displays with casters can be easily rearranged to accommodate new stock or promotional events. This adaptability helps retailers maintain a dynamic shopping environment that responds to consumer trends and seasonal changes, thus maximizing sales potential and customer satisfaction. In manufacturing, casters are crucial for transporting heavy equipment and materials. They enable seamless movement across production floors, promoting a streamlined workflow and allowing for quick adjustments to production lines.
Innovations in Caster Technology
Caster technology has not remained static; it has evolved, incorporating new materials and intelligent technology to meet modern demands. Today’s casters might include automatic locking, electric wheels, or integrated sensors communicating with smart factory systems. These smart technology advancements enable manufacturers to enhance process efficiency and proactively address maintenance needs by monitoring wear and detecting faults before they lead to significant disruptions. As casters get smarter, they contribute to the rise of fully automated and efficient production environments.
Choosing the Right Caster for Your Needs
Selection of the correct caster involves carefully considering multiple factors to ensure compatibility with your environment and requirements. Rigid casters are designed for linear movement and are perfect for applications that do not require directional changes. Conversely, swivel casters provide 360-degree rotation, offering superior maneuverability in tight spaces where agility is a priority. Locking casters, which provide mobility and stability, are ideal in environments where equipment needs to remain stationary once positioned.
Beyond motion, other factors can significantly influence caster performance. These include the surface of the floor—whether rough, smooth, or uneven—and environmental conditions, such as exposure to moisture or chemicals. Assessing weight capacity is also crucial, as choosing a caster that cannot support the load can lead to premature failure or safety hazards.
Maintenance Tips for Long-lasting Casters
Regular maintenance should be a priority to maximize the lifespan of your casters. Implementing a frequent inspection schedule allows for early detection of wear and tear, particularly on treads and bearings, which are most susceptible. It is also essential to ensure that all bolts and fasteners are tightly secured to prevent instability during use. Regular cleaning is equally important to remove debris that might accumulate in the wheels, as dirt build-up can hinder movement and accelerate wear.
Lubrication is another maintenance step that must be considered. Well-lubricated casters run smoother and quieter, prolonging their lifespan and enhancing the operator’s user experience. Developing a systematic approach to maintenance based on the environment’s specific demands can significantly reduce downtime and prevent costly replacements.
INDUSTRY
Innovations in Precision Casting for Industrial Efficiency
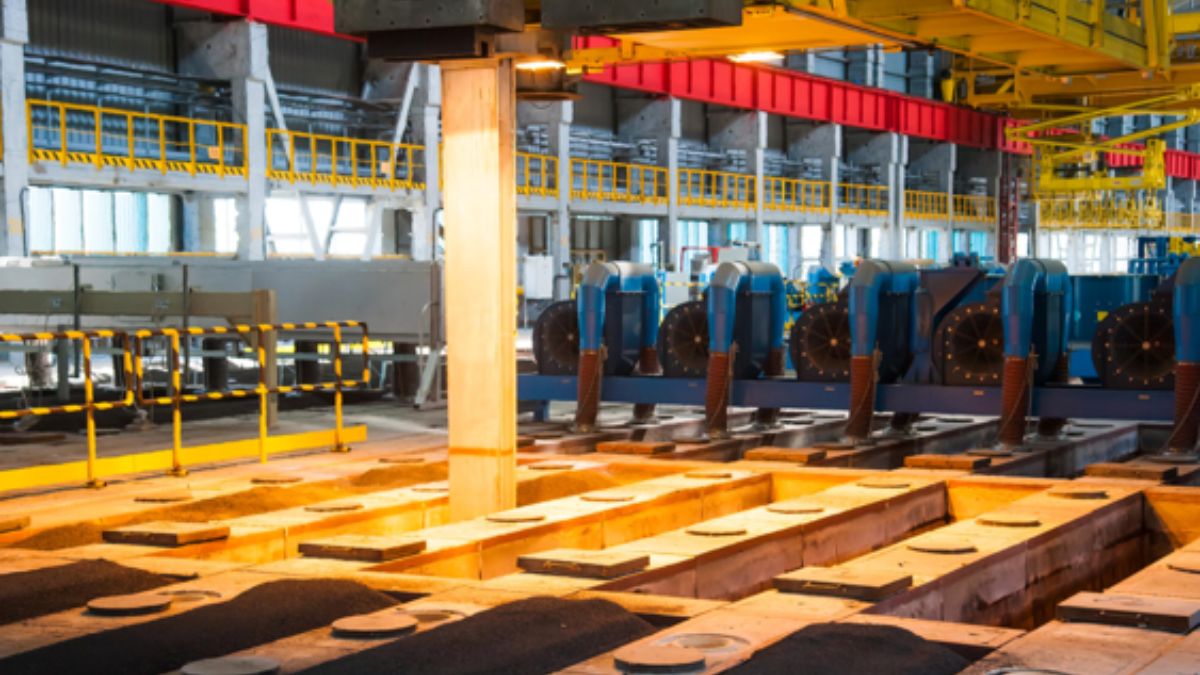
Precision casting is changing how industries create metal parts today. This method helps make strong and exact shapes with less waste. New tools and ideas make the casting process faster and better.
Factories now use less energy and fewer materials, which saves money. Precision casting also makes safer and more reliable parts.
But how do these innovations help industries every day? Let’s explore the latest improvements in precision casting and see how they improve industrial efficiency in smart and simple ways.
Advanced Mold Design Boosts Casting Accuracy
New 3D modeling tools help design better casting molds. These digital models allow engineers to test shapes before production. This process reduces errors and improves final product quality.
Less waste is produced, and parts fit better in machines. Accurate molds also save time during finishing, allowing factories to work faster without fixing small mistakes.
Improved designs also make casting safer. This innovation helps companies build strong parts with fewer steps and less effort.
Ceramic Shell Improvements for Better Results
Ceramic shells now last longer and handle heat more efficiently. These shells form around wax models to shape the final part. Stronger ceramics keep the mold from cracking during pouring.
This reduces failure and keeps the shape sharp. Better shells mean smoother surfaces on metal parts. They also help save energy during heating.
Factories can reuse shells, lowering material costs. These upgrades help workers make better parts in less time.
Robotic Pouring Systems Improve Worker Safety
Robotic systems now pour molten metal into molds with precision. This reduces the chance of burns or other accidents. Robots control the speed and angle of pouring.
These exact moves help avoid bubbles and weak spots. Robots can work in very hot areas without breaks, keeping production steady and workers safe.
Robotic pouring also limits wasted material. These smart machines improve safety and keep casting results consistent every time.
Smart Monitoring Tools for Quality Control
Sensors now check temperature, speed, and metal flow in real time. These tools catch problems before they affect the final product. They send alerts if something goes wrong during casting.
This helps workers fix mistakes right away. Less downtime means more products made each day. The sensors also gather data to improve future batches.
Quality stays high with fewer rejections. These tools help companies meet customer needs faster and smarter.
Stronger Stainless Steel Alloys Enhance Part Performance
Modern casting uses advanced stainless steel alloys for better durability. These metals resist rust, wear, and extreme temperatures very well. They are ideal for machine parts, tools, and outdoor equipment.
One popular alloy, SS304, offers both strength and a clean finish. It is often chosen for its long-lasting and safe properties.
This material reduces the need for extra coating or repair. Using strong alloys helps industries save money and boost efficiency.
Embracing Precision Casting
Innovations in precision casting are making industries work smarter today. These changes save time, improve quality, and protect workers. New tools like 3D models, sensors, and robots play a big part.
Every upgrade leads to faster and cleaner production. With fewer errors and less waste, factories become more efficient. These improvements show how smart ideas shape the future of industrial success.
Did you find this article helpful? If so, check out the rest of our site for more informative content.
INDUSTRY
The Benefits of Plate and Frame Heat Exchangers in Modern Industry
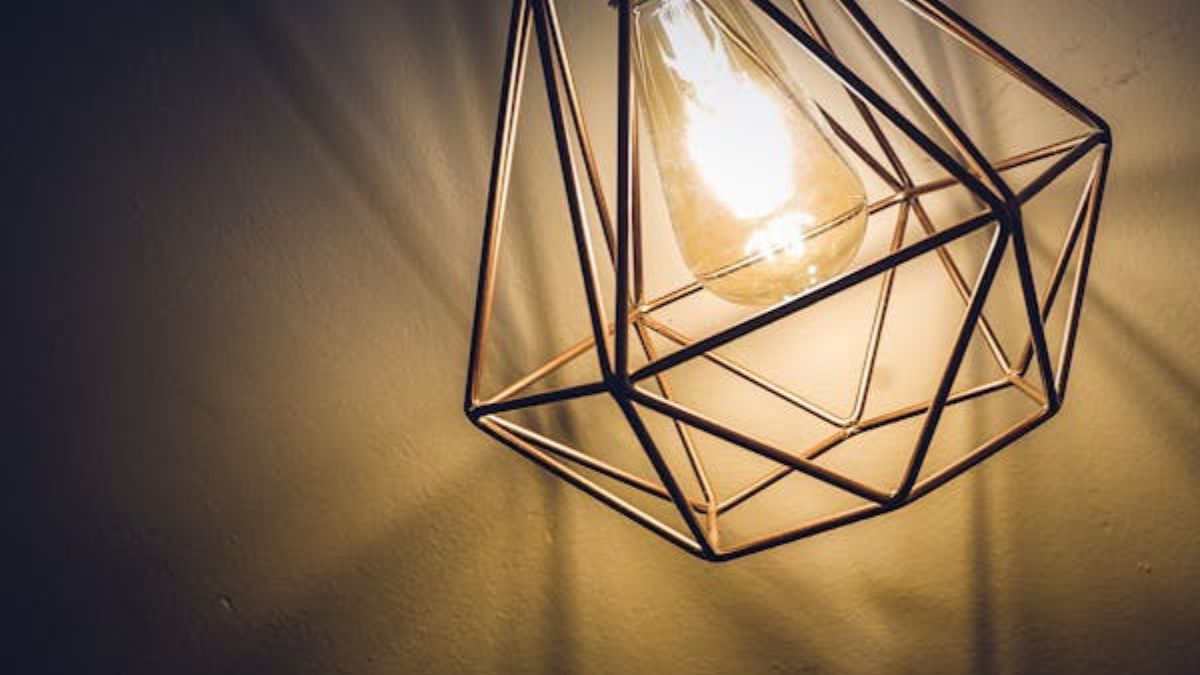
Introduction to Heat Exchangers
Heat exchangers are indispensable components in various industries, establishing themselves as vital equipment that efficiently transfers heat. By enabling the transfer of heat between two or more fluids without them coming into direct contact, heat exchangers help optimize energy usage and power industrial operations. Among the extensive range of available designs, plate and frame heat exchangers have carved out a significant niche due to their flexibility and effective performance. Their increasing popularity in plate and frame rental services testifies to their user-friendly and compact design that can easily fit into confined spaces, making them highly desirable in modern applications.
What Are Plate and Frame Heat Exchangers?
Plate and frame heat exchangers comprise a series of thin, corrugated metal plates stacked and separated by gaskets or other seals. This innovative design creates a large surface area relative to the volume, significantly enhancing their capacity to transfer heat. The alternating arrangement allows fluids to flow through the channels between the plates, maximizing their exposure to the heat transfer surfaces and facilitating an efficient and rapid heat exchange process. The configuration facilitates easy assembly and disassembly and allows for scalability, making plate and frame heat exchangers an ideal choice for diverse applications requiring varying degrees of heat transfer.
Advantages of Plate and Frame Heat Exchangers
- High Thermal Efficiency: The plates’ corrugated design generates turbulence in the fluids, augmenting the rate at which heat is transferred from one fluid to another. This inherent characteristic ensures that even small units can achieve significant temperature changes, thereby conserving energy.
- Compact Design: Plate and frame heat exchangers boast a small footprint beyond their efficiency, making them the preferred choice for locations where space is constrained. This compactness does not compromise their performance, adding to their versatility and appeal.
- Easy Maintenance: The modular design allows for the removal and cleaning of individual plates without dismantling the entire setup. This ease of maintenance reduces operational downtime and significantly cuts maintenance costs, translating into substantial savings over the equipment’s lifespan.
Applications in Various Industries
The adaptability of plate and frame heat exchangers is evident in their extensive use across various industries, including HVAC, chemical processing, food and beverage, and energy generation. Their ability to handle high-pressure and temperature situations suits them for challenging industrial environments. For instance, in the food and beverage industry, these heat exchangers are used for pasteurization and sterilization processes, aiding in the safe production of consumable goods. Feel free to delve into more industry-specific details through this informative energy.gov article about heat exchangers, which provides insights into their multifaceted applications.
Comparing with Other Types of Heat Exchangers
While traditional shell and tube heat exchangers dominate the market, plate and frame heat exchangers offer distinct advantages that are increasingly hard to overlook. Their design allows a higher heat transfer rate within a smaller space. The compactness and efficiency make them attractive in industries where operational precision and spatial efficiency are paramount. A comparative study involving other heat exchangers demonstrates why industries are shifting toward leveraging plate and frame models for specific applications.
Challenges and Solutions
Despite the numerous advantages, plate and frame heat exchangers encounter challenges, mainly fouling and gasket failures. Fouling and accumulating unwanted deposits on the plates can impair their efficiency, while gasket failures can lead to leaks. However, these issues can be mitigated effectively through regular cleaning schedules and carefully selecting gasket materials that match the operational environment. Advances in computational fluid dynamics and material sciences promise further enhancements in the durability and reliability of these systems, thereby minimizing these challenges.
Future Prospects
The future for plate and frame heat exchangers holds much promise as industries continue to push for greater efficiency and sustainability. Ongoing research focuses on optimizing plate designs and enhancing material resilience to cope with more demanding applications. Innovations are focused on creating exchangers capable of operating across a broader spectrum of temperatures and pressures, thereby rendering them essential components in the quest for sustainable energy solutions. These technological advancements ensure that plate and frame heat exchangers remain at the forefront of modern industrial practices, driving the transition to greener and more energy-efficient methodologies.
Conclusion
In conclusion, the plate and frame heat exchangers’ inherent adaptability and performance capabilities render them critical components in contemporary industry. Their ability to offer substantial cost savings through energy efficiency and reduced maintenance needs ensures their continued relevance and prominence in an era increasingly focused on sustainability and precision. As industries evolve, plate and frame heat exchangers will remain integral to achieving optimized, environmentally friendly production processes.
INDUSTRY
Warrior Met Coal (HCC): A Promising Investment in the Metallurgical Coal Sector
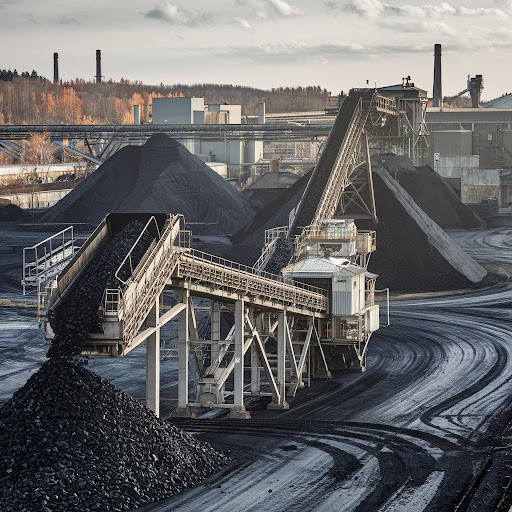
By Antonio Velardo
Antonio Velardo, a seasoned investor and analyst, highlights Warrior Met Coal (NYSE: HCC) as a standout opportunity in the metallurgical coal sector. Despite challenges faced by the industry, Velardo underscores the company’s strong fundamentals and ambitious growth project—Blue Creek—as reasons to consider it a compelling long-term investment.
Overview of Warrior Met Coal
Based in Alabama, Warrior Met Coal is a leading producer of metallurgical coal for steel production, strategically positioned to export to key markets through the McDuffie Coal Terminal in Mobile. The company currently operates two major mines, Mine No. 4 and Mine No. 7, with a combined annual production capacity of 8 million short tons. The Blue Creek project, set to commence operations in 2026, is expected to significantly boost this capacity, strengthening Warrior’s position in the global market.
Financial Strength
Warrior Met Coal’s robust financial health is one of its most appealing attributes. The company holds $709 million in cash and maintains a manageable debt level of just $171 million. This strong financial position ensures the remaining $550 million required for the Blue Creek project can be financed without jeopardizing its stability.
Blue Creek: A Game-Changer for Future Growth
The Blue Creek project is central to Warrior Met Coal’s expansion strategy. Once operational in 2026, the project is expected to greatly enhance production while reducing operating costs, driving higher margins and profitability. Although current coking coal prices have pressured margins, Velardo emphasizes that the cost efficiencies from Blue Creek will position Warrior Met Coal for substantial long-term gains.
A Strategic Entry Point
Velardo points to the recent dip in Warrior Met Coal’s stock price as an ideal entry point for investors. At an EV/EBITDA multiple of 5.0, the stock appears undervalued, as the market has not fully priced in the growth potential from the Blue Creek project.
Conclusion
Antonio Velardo views Warrior Met Coal as an undervalued opportunity in the metallurgical coal industry. With a strong balance sheet, transformative growth initiatives like Blue Creek, and an attractive valuation, the company offers significant upside for long-term investors.
The recent pullback in stock price should be seen as a chance to invest in a company poised for considerable earnings and cash flow growth by 2026-2027. Velardo emphasizes that Warrior Met Coal has a clear path to profitability and is well-positioned to become a market leader.
For investors looking to diversify their portfolios and capitalize on the potential of the coal sector, Warrior Met Coal stands out as a solid contender with a bright future.
-
HEALTH1 year ago
Integrating Semaglutide into Your Weight Loss Plan: A Practical Guide
-
HOME IMPROVEMENT1 year ago
How to Choose the Perfect Neutral Area Rug for Every Room
-
LAW1 year ago
Teenage Drivers and Car Accidents in California: Risks and Parental Liability
-
LAW1 year ago
Post-Divorce Considerations in California: Modifications and Long-Term Planning
-
CONSTRUCTION1 year ago
Construction Site Safety Regulations in New York and Your Rights as a Worker
-
HOME1 year ago
Sandra Orlow: The Teen Model Who Captivated the Internet
-
FINANCE1 year ago
Digital Asset Management in Florida Estate Planning
-
LAW1 year ago
Kentucky’s School Football: Concussions, Injuries, and Legal Options