INDUSTRY
Applications Of Rubber Washers In Industrial Machinery
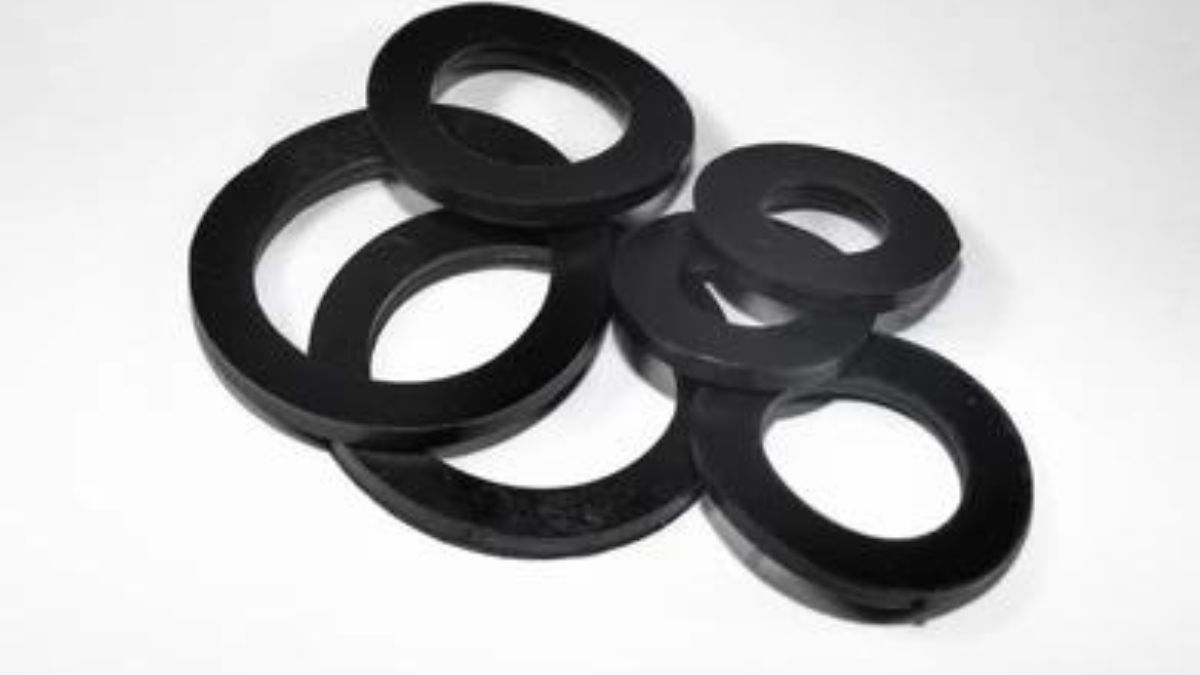
Sealing and fastening components are pivotal in industrial machinery, ensuring operational efficiency and safety. One of the unsung heroes in this category is the rubber washer.
These versatile components offer effective sealing, vibration dampening, and load distribution in many industrial applications. Their importance is best understood when one considers their role in preventing leaks, mitigating vibrations, and distributing loads evenly across surfaces.
Available in various designs and materials to meet specific industrial requirements, these washers serve multiple purposes across diverse sectors. From preventing fluid leaks in plumbing systems to reducing vibrations in high-speed manufacturing equipment, they are indispensable to maintaining machinery performance and prolonging equipment lifespan.
Purchase these washers directly from Superior Washer & Gasket.
This will provide an in-depth analysis of the different types of sealing components, their key applications, and the materials used in their manufacture to guide industries in selecting the appropriate washer for their specific needs.
Key Roles Of Washers In Industrial Applications
Sealing
Sealing is one of the primary roles of these components in industrial machinery. Creating a tight seal prevents leaks and contamination in fluid systems. Rubber sealing washers are designed to handle this function, providing reliable sealing in plumbing, hydraulic, and pneumatic systems. Their flexibility and compression properties make them ideal for ensuring leak-proof connections between metal surfaces.
Effective sealing is crucial in numerous industrial applications, where leaks can lead to operational inefficiencies and significant safety and environmental concerns. For instance, in hydraulic systems, these washers prevent hydraulic fluid leakage, ensuring proper pressure levels and minimizing the risk of catastrophic failure. Similarly, in pneumatic systems, they help maintain air pressure and prevent contamination from entering the system.
Sealing washers are commonly used in plumbing systems to ensure a watertight seal in faucets, pipes, and valves. They also play a vital role in HVAC systems, preventing refrigerant leakage and maintaining system efficiency. Given their diverse environments, sealing washers are made from materials like nitrile, EPDM, and neoprene, which offer resistance to oils, chemicals, and extreme temperatures.
Shock Absorption And Vibration Dampening
In many industrial applications, machinery operates under high loads and speeds, often leading to unwanted vibrations and shocks. These vibrations can cause equipment wear, noise, and reduced efficiency if unchecked. Thick rubber washers absorb shocks and dampen vibrations, extending the lifespan of machinery components and reducing maintenance needs.
Vibration dampening is essential in high-speed manufacturing equipment and heavy machinery, where vibrations can lead to misalignment, excessive noise, and even structural damage. If placed between the equipment and its mounting surface, vibration dampening effectively reduces these vibrations, protecting the machinery and the surrounding structures.
Shock absorption ensures smooth operation and passenger comfort in automotive and aerospace applications. Washers used in engine mounts, suspension systems, and exhaust mounts significantly reduce noise and vibrations, improving overall vehicle performance. In precision manufacturing environments, such as semiconductor production, vibration dampening is critical to maintaining product quality and minimizing defects.
Load Distribution And Surface Protection
Load distribution is crucial in preventing damage to surfaces and ensuring secure fastening. Rubber fender washers, which have a larger outer diameter than their inner diameter, are perfect for this purpose. They distribute the load over a wider area, minimizing surface damage and providing a secure hold, even under heavy loads.
Even load distribution is vital to preventing surface deformation and ensuring reliable fastening in industrial machinery. These washers are specifically designed for this purpose, with their large surface area providing optimal load distribution. They are used extensively in construction equipment, where the fasteners need to hold heavy structural components securely in place without damaging the underlying surfaces.
These washers also play a critical role in protecting surfaces. Metal-on-metal contact can lead to corrosion, galling, and surface damage when fastening metal components together. By placing rubber fender washers between these metal components, surface damage is minimized, and the machinery’s lifespan is extended.
Types Of Washers Used In Industrial Machinery
Rubber flat washers are the most common type, known for their versatility and efficiency in providing tight seals. They are widely used in pipe connections, hydraulic equipment, and general fastening applications where sealing and vibration dampening are required.
These components are available in a wide range of diameters and thicknesses, making them suitable for various applications. They are often used in plumbing systems to prevent leaks in pipe connections and faucets. In hydraulic systems, these washers ensure leak-proof seals between fittings, preventing fluid loss and maintaining system efficiency.
In general, fastening applications provide a cushioning effect, reducing vibration and preventing fastener loosening due to movement. They also protect surfaces from damage by distributing the load evenly.
Rubber Sealing Washers
These washers are specifically designed for high-performance sealing in fluid systems. Their unique properties, such as resistance to oils and chemicals, make them suitable for plumbing and HVAC systems.
Sealing washers are often used in plumbing systems to prevent leaks in faucets, valves, and pipe connections. They are also crucial in HVAC systems, ensuring airtight and watertight seals to maintain system efficiency.
These components are used in plumbing, HVAC systems, automotive, and aerospace applications. They provide reliable sealing in fuel systems, engines, and other fluid systems, and their resistance to oils, fuels, and chemicals makes them ideal for these demanding environments.
Due to their increased thickness, thick rubber washers offer superior shock absorption and vibration dampening. They are used in machinery where minimizing noise and protecting sensitive equipment from shocks are priorities.
These components are commonly used in manufacturing equipment, absorbing vibration and shocks generated by high-speed machinery. By reducing vibrations, these washers protect sensitive equipment from misalignment and damage, ensuring smooth operation and extending equipment lifespan.
In the automotive industry, they are used in engine mounts, suspension systems, and exhaust mounts to absorb vibrations and shocks, improving ride comfort and reducing noise. In construction equipment, they provide cushioning and vibration dampening in heavy machinery, ensuring secure operation under extreme loads.
Rubber fender washers have a larger outer diameter, providing a greater surface area for load distribution. They are used in applications where surface protection and secure fastening are critical, such as construction equipment and large machinery.
Fender washers are designed to distribute the load over a wider area, preventing surface damage and ensuring reliable fastening. They secure heavy structural components in construction equipment while minimizing surface damage. They are also used in manufacturing equipment, protecting surfaces from scratches and dents caused by metal-on-metal contact.
In addition to load distribution, they provide a cushioning effect, reducing vibration and preventing fastener loosening due to movement. Their resistance to weathering and chemicals makes them suitable for outdoor applications, such as securing signs and panels.
Black Rubber Washers & Versatility
These are versatile components often used in general-purpose sealing and fastening applications. Their black color is aesthetically pleasing and suitable for visible installations where appearance matters.
These components are made from neoprene and EPDM, offering resistance to weathering, oils, and chemicals. They are used in automotive applications where aesthetic concerns matter, such as securing trim and body panels. In plumbing systems, black rubber washers provide a neat finish to visible connections.
Their versatility makes these washers suitable for various applications, including electrical installations, furniture assembly, and general maintenance.
Material Considerations In Selecting Washers
Nitrile Rubber (NBR)
Nitrile rubber is known for its resistance to oils, fuels, and chemicals. This makes it ideal for rubber sealing washers used in hydraulic and fuel systems where oil resistance is crucial.
Nitrile rubber, also known as Buna-N, is widely used in industrial machinery due to its excellent resistance to petroleum-based oils, fuels, and chemicals. They are made from nitrile rubber and are commonly used in hydraulic systems to prevent leaks and maintain pressure. In fuel systems, they provide a reliable seal, preventing fuel leaks and ensuring safe operation.
In addition to hydraulic and fuel systems, nitrile rubber washers are used in plumbing systems, where they resist degradation from oils and chemicals. Their excellent compression set resistance ensures a tight seal even under high pressure.
Neoprene Washers
Neoprene is a versatile material that is resistant to weathering, oils, and chemicals. Black rubber washers made from neoprene are popular due to their resilience and aesthetic appeal.
Neoprene rubber washers are widely used in industrial machinery due to their resistance to weathering, oils, and chemicals. They are often used in outdoor applications where UV rays and ozone resistance is crucial. In plumbing systems, neoprene washers provide reliable sealing and cushioning, ensuring leak-proof connections.
In automotive applications, black neoprene washers secure trim and body panels while resisting oils and chemicals. Their resilience makes them suitable for applications requiring repeated compression, such as door seals and gaskets.
EPDM
EPDM rubber excels at resisting ozone, UV rays, and extreme temperatures, making it suitable for outdoor applications. EPDM rubber flat washers and fender washers are ideal for applications where weather resistance is essential.
EPDM rubber is known for its excellent resistance to ozone, UV rays, and extreme temperatures. They are made from EPDM and are widely used in outdoor applications where weather resistance is crucial. In construction equipment, EPDM washers secure structural components while resisting degradation from sunlight and ozone.
EPDM washers provide reliable sealing and cushioning in plumbing systems, ensuring leak-proof connections even in hot water applications. Their excellent temperature resistance makes them suitable for HVAC systems, where they prevent refrigerant leaks and maintain system efficiency.
Silicone Rubber
Silicone rubber offers excellent high-temperature resistance and flexibility. Thick silicone rubber washers are perfect for vibration-dampening applications in high-temperature environments.
Silicone rubber is known for its high-temperature resistance and flexibility, making it ideal for washers used in high-temperature environments. In manufacturing equipment, silicone washers provide vibration dampening and shock absorption while withstanding temperatures up to 200°C.
In automotive and aerospace applications, silicone washers are used in engine mounts, exhaust mounts, and other high-temperature components. Their flexibility ensures a tight seal, even under extreme temperature fluctuations, while their high-temperature resistance prevents degradation.
Applications In Specific Industries
Oil And Gas
The oil and gas industry requires robust sealing solutions due to the harsh environments and stringent safety standards. Rubber sealing washers made from nitrile rubber prevent leaks in pipelines and drilling equipment by providing an oil-resistant seal.
Sealing is crucial in the oil and gas industry to prevent leaks and ensure safe operation. Nitrile rubber washers provide reliable sealing in pipelines, drilling equipment, and refining units. Their resistance to oils, fuels, and chemicals ensures leak-proof connections in harsh environments.
In addition to sealing, components provide vibration dampening and shock absorption in drilling equipment, reducing noise and protecting sensitive components from damage. They also offer load distribution and surface protection, ensuring secure fastening in heavy machinery.
Manufacturing And Production Lines
Manufacturing and production lines often involve high-speed machinery that can generate significant vibrations. Thick rubber washers provide shock absorption and vibration dampening to protect equipment and maintain efficiency.
Vibration from high-speed machinery in manufacturing and production lines can lead to misalignment, excessive noise, and equipment damage. They provide effective shock absorption and vibration dampening, ensuring smooth operation and reducing maintenance needs.
Placing these washers between the machinery and its mounting surface reduces vibration, protecting sensitive components and surrounding structures. These washers also minimize noise, improving the working environment and preventing hearing damage.
In precision manufacturing environments, such as semiconductor production, vibration dampening is crucial to maintaining product quality and minimizing defects. These washers provide the necessary cushioning and stability to ensure consistent production.
Construction Equipment
Construction equipment frequently operates under heavy loads. Rubber fender washers distribute these loads evenly and protect surfaces from damage, ensuring the longevity and stability of connections in construction machinery.
Load distribution is essential in construction equipment to prevent surface damage and ensure secure fastening. Large outer diameters provide a wider surface area for load distribution. They secure heavy structural components while minimizing surface damage.
These washers provide cushioning and vibration dampening in heavy machinery, ensuring secure operation under extreme loads. Their resistance to weathering and chemicals makes them suitable for outdoor applications, such as securing panels and signs.
Washers in construction equipment also play a critical role in surface protection. Placing them between metal components minimizes surface damage, extending the machinery’s lifespan and reducing maintenance needs.
Automotive And Aerospace
The automotive and aerospace industries require components that can withstand rigorous operational conditions. Rubber flat washers and black rubber washers are used in these industries for efficient sealing and vibration dampening, ensuring safety and reliability.
Components are used in various applications in the automotive and aerospace industries to provide sealing, cushioning, and vibration dampening. These washers are commonly used in fuel systems, engines, and suspension systems to prevent leaks and reduce noise.
In engine and exhaust mounts, thick rubber washers absorb vibrations and shocks, improving ride comfort and reducing noise. Rubber sealing washers ensure airtight and watertight seals in fuel systems and engines, preventing leaks and maintaining system efficiency.
In aerospace applications, where weight and reliability are critical, these washers provide lightweight sealing and cushioning solutions. Their resistance to extreme temperatures and chemicals ensures reliable performance even in demanding environments.
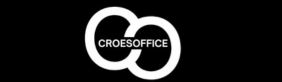
INDUSTRY
Innovations in Precision Casting for Industrial Efficiency
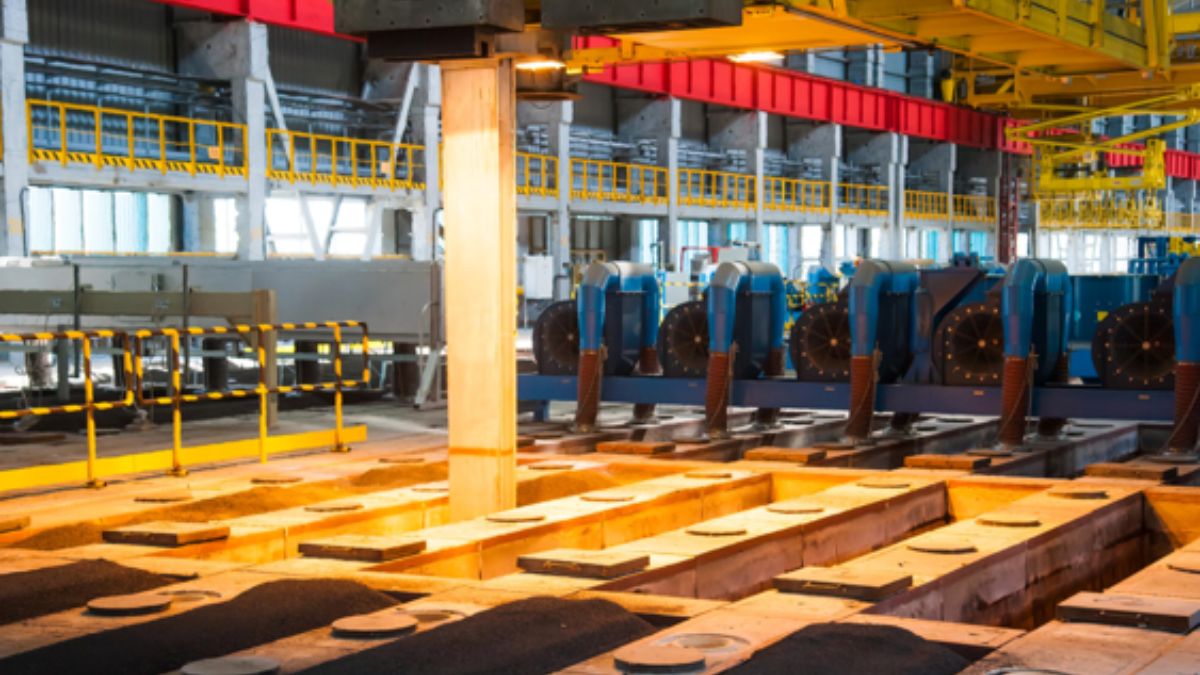
Precision casting is changing how industries create metal parts today. This method helps make strong and exact shapes with less waste. New tools and ideas make the casting process faster and better.
Factories now use less energy and fewer materials, which saves money. Precision casting also makes safer and more reliable parts.
But how do these innovations help industries every day? Let’s explore the latest improvements in precision casting and see how they improve industrial efficiency in smart and simple ways.
Advanced Mold Design Boosts Casting Accuracy
New 3D modeling tools help design better casting molds. These digital models allow engineers to test shapes before production. This process reduces errors and improves final product quality.
Less waste is produced, and parts fit better in machines. Accurate molds also save time during finishing, allowing factories to work faster without fixing small mistakes.
Improved designs also make casting safer. This innovation helps companies build strong parts with fewer steps and less effort.
Ceramic Shell Improvements for Better Results
Ceramic shells now last longer and handle heat more efficiently. These shells form around wax models to shape the final part. Stronger ceramics keep the mold from cracking during pouring.
This reduces failure and keeps the shape sharp. Better shells mean smoother surfaces on metal parts. They also help save energy during heating.
Factories can reuse shells, lowering material costs. These upgrades help workers make better parts in less time.
Robotic Pouring Systems Improve Worker Safety
Robotic systems now pour molten metal into molds with precision. This reduces the chance of burns or other accidents. Robots control the speed and angle of pouring.
These exact moves help avoid bubbles and weak spots. Robots can work in very hot areas without breaks, keeping production steady and workers safe.
Robotic pouring also limits wasted material. These smart machines improve safety and keep casting results consistent every time.
Smart Monitoring Tools for Quality Control
Sensors now check temperature, speed, and metal flow in real time. These tools catch problems before they affect the final product. They send alerts if something goes wrong during casting.
This helps workers fix mistakes right away. Less downtime means more products made each day. The sensors also gather data to improve future batches.
Quality stays high with fewer rejections. These tools help companies meet customer needs faster and smarter.
Stronger Stainless Steel Alloys Enhance Part Performance
Modern casting uses advanced stainless steel alloys for better durability. These metals resist rust, wear, and extreme temperatures very well. They are ideal for machine parts, tools, and outdoor equipment.
One popular alloy, SS304, offers both strength and a clean finish. It is often chosen for its long-lasting and safe properties.
This material reduces the need for extra coating or repair. Using strong alloys helps industries save money and boost efficiency.
Embracing Precision Casting
Innovations in precision casting are making industries work smarter today. These changes save time, improve quality, and protect workers. New tools like 3D models, sensors, and robots play a big part.
Every upgrade leads to faster and cleaner production. With fewer errors and less waste, factories become more efficient. These improvements show how smart ideas shape the future of industrial success.
Did you find this article helpful? If so, check out the rest of our site for more informative content.
INDUSTRY
The Benefits of Plate and Frame Heat Exchangers in Modern Industry
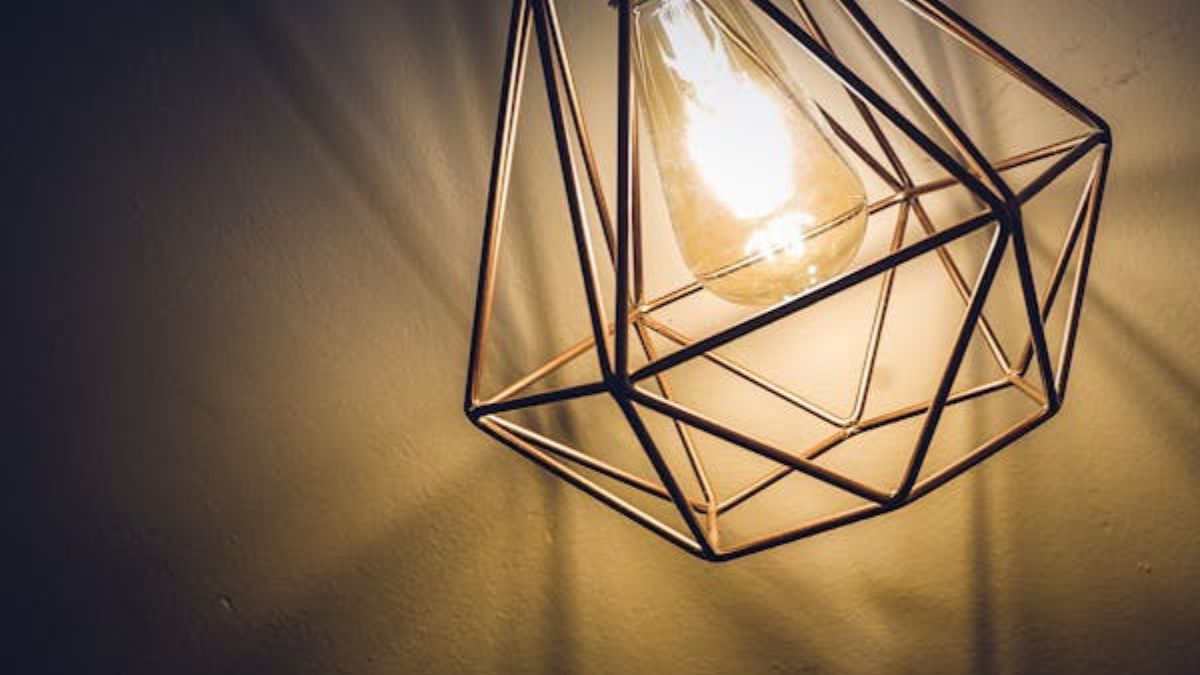
Introduction to Heat Exchangers
Heat exchangers are indispensable components in various industries, establishing themselves as vital equipment that efficiently transfers heat. By enabling the transfer of heat between two or more fluids without them coming into direct contact, heat exchangers help optimize energy usage and power industrial operations. Among the extensive range of available designs, plate and frame heat exchangers have carved out a significant niche due to their flexibility and effective performance. Their increasing popularity in plate and frame rental services testifies to their user-friendly and compact design that can easily fit into confined spaces, making them highly desirable in modern applications.
What Are Plate and Frame Heat Exchangers?
Plate and frame heat exchangers comprise a series of thin, corrugated metal plates stacked and separated by gaskets or other seals. This innovative design creates a large surface area relative to the volume, significantly enhancing their capacity to transfer heat. The alternating arrangement allows fluids to flow through the channels between the plates, maximizing their exposure to the heat transfer surfaces and facilitating an efficient and rapid heat exchange process. The configuration facilitates easy assembly and disassembly and allows for scalability, making plate and frame heat exchangers an ideal choice for diverse applications requiring varying degrees of heat transfer.
Advantages of Plate and Frame Heat Exchangers
- High Thermal Efficiency: The plates’ corrugated design generates turbulence in the fluids, augmenting the rate at which heat is transferred from one fluid to another. This inherent characteristic ensures that even small units can achieve significant temperature changes, thereby conserving energy.
- Compact Design: Plate and frame heat exchangers boast a small footprint beyond their efficiency, making them the preferred choice for locations where space is constrained. This compactness does not compromise their performance, adding to their versatility and appeal.
- Easy Maintenance: The modular design allows for the removal and cleaning of individual plates without dismantling the entire setup. This ease of maintenance reduces operational downtime and significantly cuts maintenance costs, translating into substantial savings over the equipment’s lifespan.
Applications in Various Industries
The adaptability of plate and frame heat exchangers is evident in their extensive use across various industries, including HVAC, chemical processing, food and beverage, and energy generation. Their ability to handle high-pressure and temperature situations suits them for challenging industrial environments. For instance, in the food and beverage industry, these heat exchangers are used for pasteurization and sterilization processes, aiding in the safe production of consumable goods. Feel free to delve into more industry-specific details through this informative energy.gov article about heat exchangers, which provides insights into their multifaceted applications.
Comparing with Other Types of Heat Exchangers
While traditional shell and tube heat exchangers dominate the market, plate and frame heat exchangers offer distinct advantages that are increasingly hard to overlook. Their design allows a higher heat transfer rate within a smaller space. The compactness and efficiency make them attractive in industries where operational precision and spatial efficiency are paramount. A comparative study involving other heat exchangers demonstrates why industries are shifting toward leveraging plate and frame models for specific applications.
Challenges and Solutions
Despite the numerous advantages, plate and frame heat exchangers encounter challenges, mainly fouling and gasket failures. Fouling and accumulating unwanted deposits on the plates can impair their efficiency, while gasket failures can lead to leaks. However, these issues can be mitigated effectively through regular cleaning schedules and carefully selecting gasket materials that match the operational environment. Advances in computational fluid dynamics and material sciences promise further enhancements in the durability and reliability of these systems, thereby minimizing these challenges.
Future Prospects
The future for plate and frame heat exchangers holds much promise as industries continue to push for greater efficiency and sustainability. Ongoing research focuses on optimizing plate designs and enhancing material resilience to cope with more demanding applications. Innovations are focused on creating exchangers capable of operating across a broader spectrum of temperatures and pressures, thereby rendering them essential components in the quest for sustainable energy solutions. These technological advancements ensure that plate and frame heat exchangers remain at the forefront of modern industrial practices, driving the transition to greener and more energy-efficient methodologies.
Conclusion
In conclusion, the plate and frame heat exchangers’ inherent adaptability and performance capabilities render them critical components in contemporary industry. Their ability to offer substantial cost savings through energy efficiency and reduced maintenance needs ensures their continued relevance and prominence in an era increasingly focused on sustainability and precision. As industries evolve, plate and frame heat exchangers will remain integral to achieving optimized, environmentally friendly production processes.
INDUSTRY
Warrior Met Coal (HCC): A Promising Investment in the Metallurgical Coal Sector
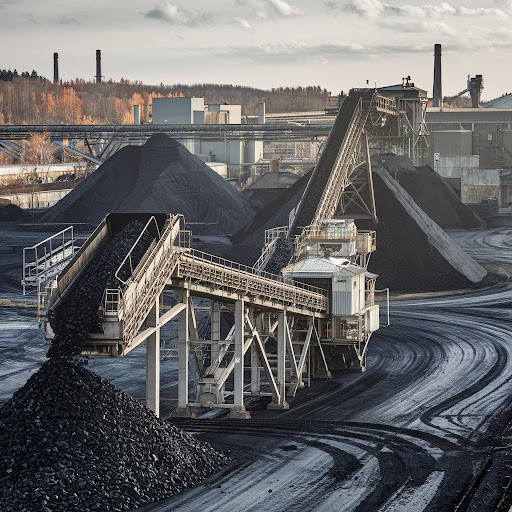
By Antonio Velardo
Antonio Velardo, a seasoned investor and analyst, highlights Warrior Met Coal (NYSE: HCC) as a standout opportunity in the metallurgical coal sector. Despite challenges faced by the industry, Velardo underscores the company’s strong fundamentals and ambitious growth project—Blue Creek—as reasons to consider it a compelling long-term investment.
Overview of Warrior Met Coal
Based in Alabama, Warrior Met Coal is a leading producer of metallurgical coal for steel production, strategically positioned to export to key markets through the McDuffie Coal Terminal in Mobile. The company currently operates two major mines, Mine No. 4 and Mine No. 7, with a combined annual production capacity of 8 million short tons. The Blue Creek project, set to commence operations in 2026, is expected to significantly boost this capacity, strengthening Warrior’s position in the global market.
Financial Strength
Warrior Met Coal’s robust financial health is one of its most appealing attributes. The company holds $709 million in cash and maintains a manageable debt level of just $171 million. This strong financial position ensures the remaining $550 million required for the Blue Creek project can be financed without jeopardizing its stability.
Blue Creek: A Game-Changer for Future Growth
The Blue Creek project is central to Warrior Met Coal’s expansion strategy. Once operational in 2026, the project is expected to greatly enhance production while reducing operating costs, driving higher margins and profitability. Although current coking coal prices have pressured margins, Velardo emphasizes that the cost efficiencies from Blue Creek will position Warrior Met Coal for substantial long-term gains.
A Strategic Entry Point
Velardo points to the recent dip in Warrior Met Coal’s stock price as an ideal entry point for investors. At an EV/EBITDA multiple of 5.0, the stock appears undervalued, as the market has not fully priced in the growth potential from the Blue Creek project.
Conclusion
Antonio Velardo views Warrior Met Coal as an undervalued opportunity in the metallurgical coal industry. With a strong balance sheet, transformative growth initiatives like Blue Creek, and an attractive valuation, the company offers significant upside for long-term investors.
The recent pullback in stock price should be seen as a chance to invest in a company poised for considerable earnings and cash flow growth by 2026-2027. Velardo emphasizes that Warrior Met Coal has a clear path to profitability and is well-positioned to become a market leader.
For investors looking to diversify their portfolios and capitalize on the potential of the coal sector, Warrior Met Coal stands out as a solid contender with a bright future.
-
HEALTH1 year ago
Integrating Semaglutide into Your Weight Loss Plan: A Practical Guide
-
HOME IMPROVEMENT1 year ago
How to Choose the Perfect Neutral Area Rug for Every Room
-
LAW1 year ago
Teenage Drivers and Car Accidents in California: Risks and Parental Liability
-
LAW1 year ago
Post-Divorce Considerations in California: Modifications and Long-Term Planning
-
CONSTRUCTION1 year ago
Construction Site Safety Regulations in New York and Your Rights as a Worker
-
HOME1 year ago
Sandra Orlow: The Teen Model Who Captivated the Internet
-
FINANCE1 year ago
Digital Asset Management in Florida Estate Planning
-
LAW1 year ago
Kentucky’s School Football: Concussions, Injuries, and Legal Options